Episode 97: Industrial AI
Augmented Ops - Un pódcast de Tulip - Miercoles
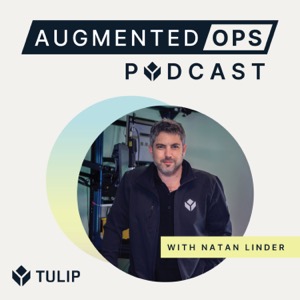
Categorías:
Augmented reveals the stories behind the new era of industrial operations, where technology will restore the agility of frontline workers. The topic is Industrial AI. Our guest is Professor Jay Lee, the Ohio Eminent Scholar, the L.W. Scott Alter Chair Professor in Advanced Manufacturing, and the Founding Director of the Industrial AI Center at the University of Cincinnati. In this conversation, we talk about how AI does many things but to be applicable; the industry needs it to work every time, which puts additional constraints on what can be done by when. If you liked this show, subscribe at augmentedpodcast.co. If you liked this episode, you might also like Episode 81: From Predictive to Diagnostic Manufacturing Augmentation. Augmented is a podcast for industry leaders, process engineers, and shop floor operators, hosted by futurist Trond Arne Undheim and presented by Tulip. Follow the podcast on Twitter or LinkedIn. Trond's Takeaway: Industrial AI is a breakthrough that will take a while to mature. It implies discipline, not just algorithms. In fact, it entails a systems architecture consisting of data, algorithm, platform, and operation. Transcript: TROND: Welcome to another episode of the Augmented Podcast. Augmented brings industrial conversations that matter, serving up the most relevant conversations on industrial tech. Our vision is a world where technology will restore the agility of frontline workers. In this episode of the podcast, the topic is Industrial AI. Our guest is Professor Jay Lee, the Ohio Eminent Scholar, and the L.W. Scott Alter Chair Professor in Advanced Manufacturing, and the Founding Director of the Industrial AI Center at the University of Cincinnati. In this conversation, we talk about how AI does many things but to be applicable, industry needs it to work every time, which puts on additional constraints on what can be done by when. Augmented is a podcast for industrial leaders, process engineers, and shop floor operators hosted by futurist Trond Arne Undheim and presented by Tulip. Jay, it's a pleasure to have you here. How are you today? JAY: Good. Thank you for inviting me to have a good discussion about industrial AI. TROND: Yeah, I think it will be a good discussion. Look, Jay, you are such an accomplished person, both in terms of your academics and your industrial credentials. I wanted to quickly just go through where you got to where you are because I think, especially in your case, it's really relevant to the kinds of findings and the kinds of exploration that you're now doing. You started out as an engineer. You have a dual degree. You have a master's in industrial management also. And then you had a career in industry, worked at real factories, GM factories, Otis elevators, and even on Sikorsky helicopters. You had that background, and then you went on to do a bunch of different NSF grants. You got yourself; I don't know, probably before that time, a Ph.D. in mechanical engineering from Columbia. The rest of your career, and you correct me, but you've been doing this mix of really serious industrial work combined with academics. And you've gone a little bit back and forth. Tell me a little bit about what went into your mind as you were entering the manufacturing topics and you started working in factories. Why have you oscillated so much between industry and practice? And tell me really this journey; give me a little bit of specifics on what brought you on this journey and where you are today. JAY: Well, thank you for talking about this career because I cut my teeth from the factory early years. And so, I learned a lot of fundamental things in early years of automation. In the early 1980s, in the U.S, it was a tough time trying to compete with the Japanese automotive industry. So, of course, the Big Three in Detroit certainly took a big giant step, tried to implement a very good manufacturing automation system. So I was working for Robotics Vision System at that time in New York, in Hauppage, New York, Long Island. And shortly, later on, it was invested by General Motors. And in the meantime, I was studying part-time in Columbia for my mechanical engineering, Doctor of Engineering. And, of course, later on, I transferred to George Washington because I had to make a career move. So I finished my Ph.D. Doctor of Science in George Washington later. But the reason we stopped working on that is because of the shortage of knowledge in making automation work in the factory. So I was working full-time trying to implement the robots automation in a factory. In the meantime, I also found a lack of knowledge on how to make a robot work and not just how to make a robot move. Making it move means you can program; you can do very fancy motion. But that's not what factories want. What factories really want is a non-stop working system so they can help people to accomplish the job. So the safety, and the certainty, the accuracy, precision, maintenance, all those things combined together become a headache actually. You have to calibrate the robot all the time. You have to reprogram them. So eventually, I was teaching part-time in Stony Brook also later on how to do the robotic stuff. And I think that was the early part of my career. And most of the time I spent in factory and still in between the part-time study and part-time working. But later on, I got a chance to move to Washington, D.C. I was working for U.S. Postal Service headquarters as Program Director for automation. In 1988, post service started a big initiative trying to automate a 500 mil facility in the U.S. There are about 115 number one facilities which is like New York handled 8 million mail pieces per day at that time; you're talking about '88. But most are manual process, so packages. So we started developing the AI pattern recognition, hand-written zip code recognition, robotic postal handling, and things like that. So that was the opportunity that attracted me actually to move away from automotive to service industry. So it was interesting because you are working with top scientists from different universities, different companies to make that work. So that was the early stage of the work. Later on, of course, I had a chance to work with the National Science Foundation doing content administration in 1991. That gave me the opportunity to work with professors in universities, of course. So then, by working with them, I was working on a lot of centers like engineering research centers and also the Industry-University Cooperative Research Centers Program, and later on, the materials processing manufacturing programs. So 1990 was a big time for manufacturing in the United States. A lot of government money funded the manufacturer research, of course. And so we see great opportunity, like, for example, over the years, all the rapid prototyping started in 1990s. It took about 15-20 years before additive manufacturing came about. So NSF always looks 20 years ahead, which is a great culture, great intellectual driver. And also, they're open to the public in terms of the knowledge sharing and the talent and the education. So I think NSF has a good position to provide STEM education also to allow academics, professors to work with industry as well, not just purely academic work. So we support both sides. So that work actually allowed me to understand what is real status in research, in academics, also how far from real implementation. So in '95, I had the opportunity to work in Japan actually. I had an opportunity...NSF had a collaboration program with the MITI government in Japan. So I took the STA fellowship called science and technology fellow, STA, and to work in Japan for six months and to work with 55 organizations like Toyota, Komatsu, Nissan, FANUC, et cetera. So by working with them, then you also understand what the real technology level Japan was, Japanese companies were. So then you got calibration in terms of how much U.S. manufacturing? How much Japanese manufacturing? So that was in my head, actually. I had good weighting factors to see; hmm, what's going on here between these two countries? That was the time. So when I came back, I said, oh, there's something we have to do differently. So I started to get involved in a lot of other things. In 1998, I had the opportunity to work for United Technologies because UTC came to see me and said, "Jay, you should really apply what you know to real companies." So they brought me to work as a Director for Product Environment Manufacturing Department for UTRC, United Technology Research Center, in East Hartford. Obviously, UTC business included Pratt & Whitney jet engines, Sikorsky helicopters, Otis elevators, Carrier Air Conditioning systems, Hamilton Sundstrand, et cetera. So all the products they're worldwide, but the problem is you want to support global operations. You really need not just the knowledge, what you know, but also the physical usage, what you don't know. So you know, and you don't know. So how much you don't know about a product usage, that's how the data is supposed to be coming back. Unfortunately, back in 1999, I have to tell you; unfortunately, most of the product data never came back. By the time it got back, it is more like a repair overhaul recur every year to a year later. So that's not good. So in Japan, I was experimenting the first remote machine monitoring system using the internet actually in 1995. So I published a paper in '98 about how to remotely use physical machine and cyber machine together. In fact, I want to say that's the first digital twin but as a cyber-physical model together. That was in my paper in 1998 in Journal of Machine Tools and Manufacture. TROND: So, in fact, you were a precursor in so many of these fields. And it just strikes me that as you're going through your career here, there are certain pieces that you seem to have learned all along the way because when you are a career changer oscillating between public, private, semi-private, research, business, you obviously run the risk of being a dilettante in every field, but you seem to have picked up just enough to get on top of the next job with some insight that others didn't have. And then, when you feel like you're frustrated in that current role, you jump back or somewhere else to learn something new. It's fascinating to me because, obviously, your story is longer than this. You have startup companies with your students and others in this business and then, of course, now with the World Economic Forum Lighthouse factories and the work you've been doing for Foxconn as well. So I'm just curious. And then obviously, we'll get to industrial AI, which is so interesting in your perspective here because it's not just the technology of it; it is the industrial practice of this new domain that you have this very unique, practical experience of how a new technology needs to work. Well, you tell me, how did you get to industrial AI? Because you got there to, you know, over the last 15-20 years, you integrated all of this in a new academic perspective. JAY: Well, that's where we start. So like I said earlier, I realized industry we did not have data back in the late 1990s. And in 1999, dotcom collapsed, remember? TROND: Yes, yes. JAY: Yeah. So all the companies tried to say, "Well, we're e-business, e-business, e-commerce, e-commerce," then in 2000, it collapsed. But the reality is that people were talking about e-business, but in the real world, in industrial setting, there's no data almost. So I was thinking, I mean, it's time I need to think about how to look at data-centric perspectives, how to develop such a platform, and also analytics to support if one-day data comes with a worry-free kind of environment. So that's why I decided to transition to an academic career in the year 2000. So what I started thinking, in the beginning, was where has the most data? As we all know, the product lifecycle usage is out there. You have lots of data, but we're not collecting it. So eventually, I called a central Intelligent Maintenance System called IMS, not intelligent manufacturing system because maintenance has lots of usage data which most developers of a product don't know. But if we have a way to collect this data to analyze and predict, then we can guarantee the product uptime or the value creation, and then the customer will gain most of the value back. Now we can use the data feedback to close-loop design. That was the original thinking back in the year 2000, which at that time, no cell phone could connect to the internet. Of course, nobody believed you. So we used a term called near-zero downtime, near-zero downtime, ZDT. Nobody believed us. Intel was my first founding member. So I made a pitch to FANUC in 2001. Of course, they did not believe it either. Of course, FANUC in 2014 adopted ZDT, [laughs] ZDT as a product name. But as a joke, when I talked to the chairman, the CEO of the company in 2018 in Japan, Inaba-san that "Do you know first we present this ZDT to your company in Michigan? They didn't believe it. Now you guys adopted." "Oh, I didn't know you use it." So when he came to visit in 2019, they brought the gift. [laughs] So anyway, so what happened is during the year, so we worked with the study of 6 companies, 20 companies and eventually they became over 100 companies. And in 2005, I worked with Procter & Gamble and GE Aircraft Engine. They now became GE Aviation; then, they got a different environment. So machine learning became a typical thing you use every day, every program, but we don't really emphasize AI at that time. The reason is machine learning is just a tool. It's an algorithm like a support-vector machine, self-organizing map, and logistic regression. All those are just supervised learning or now supervised learning techniques. And people use it. We use it like standard work every day, but we don't talk about AI. But over the years, when you work with so many companies, then you realize the biggest turning point was Toyota 2005 and P&G in 2006. The reason I'm telling you 2005 is Toyota had big problems in the factory in Georgetown, Kentucky, where the Camry factory is located. So they had big compressor problems. So we implemented using machine learning, the support-vector machine, and also principal component analysis. And we enable that the surge of a compressor predicted and avoided and never happened. So until today -- TROND: So they have achieved zero downtime after that project, essentially. JAY: Yeah. So that really is the turning point. Of course, at P&G, the diaper line continues moving the high volume. They can predict things, reduce downtime to 1%. There's a lot of money. Diaper business that is like $10 billion per year. TROND: It's so interesting you focus on downtime, Jay, because obviously, in this hype, which we'll get to as well, people seem to focus so much on fully automated versus what you're saying, which is it doesn't really, you know, we will get to the automation part, but it is the downtime that's where a lot of the savings is obviously. Because whether it's a lights out or lights on, humans are not the real saving here. And the real accomplishment is in zero downtime because that is the industrialization factor. And that is what allows the system to keep operating. Of course, it has to do with automation, but it's not just that. Can you then walk us through what then became industrial AI for you? Because as I've now understood it, it is a highly specific term to you. It's not just some sort of fluffy idea of very, very advanced algorithms and robots running crazy around autonomously. You have very, very specific system elements. And they kind of have to work together in some architectural way before you're willing to call it an industrial AI because it may be a machine tool here, and a machine tool there, and some data here. But for you, unless it's put in place in a working architecture, you're not willing to call it, I mean, it may be an AI, but it is not an industrial AI. So how did this thinking then evolve for you? And what are the elements that you think are crucial for something that you even can start to call an industrial AI? Which you now have a book on, so you're the authority on the subject. JAY: Well, I think the real motivation was after you apply all the machine learning toolkits so long...and a company like National Instruments, NI, in Austin, Texas, they licensed our machine learning toolkits in 2015. And eventually, in 2017, they started using the embedding into LabVIEW version. So we started realizing, actually, the toolkit is very important, not just from the laboratory point of view but also from the production and practitioners' point of view from industry. Of course, researchers use it all the time for homework; I mean, that’s fine. So eventually, I said...the question came to me about 2016 in one of our industry advisory board meeting. You have so many successes, but the successes that happen can you repeat? Can you repeat? Can you repeatably have the same success in many, many other sites? Repeatable, scalable, sustainable, that's the key three keywords. You cannot just have a one-time success and then just congratulate yourself and forget it, no. So eventually, we said, oh, to make that repeat sustainable, repeatable, you have a systematic discipline. TROND: I'm so glad you say this because I have taken part in a bunch of best practice schemes and sometimes very optimistically by either an industry association or even a government entity. And they say, "Oh yeah, let's just all go on a bunch of factory visits." Or if it's just an IT system, "Let's just all write down what we did, and then share it with other people." But in fact, it doesn't seem to me like it is that easy. It's not like if I just explain what I think I have learned; that's not something others can learn from. Can you explain to me what it really takes to make something replicable? Because you have done that or helped Foxconn do that, for example. And now you're obviously writing up case studies that are now shared in the World Economic Forum across companies. But there's something really granular but also something very systemic and structured about the way things have to be explained in order to actually make it repeatable. What is the sustainability factor that actually is possible to not just blue copy but turn it into something in your own factory? JAY: Well, I think that there are basically several things. The data is one thing. We call it the data technology, DT, and which means data quality evaluation. How do you understand what to use, what not to use? How do you know which data is useful? And how do you know where the data is usable? It doesn't mean useful data is usable, just like you have a blood donation donor, but the blood may not be usable if the donor has HIV. I like to use an analogy like food. You got a fish in your hand; wow, great. But you have to ask where the fish comes from. [chuckles] If it comes from polluted water, it's not edible, right? So great fish but not edible. TROND: So there's a data layer which has to be usable, and it has to be put somewhere and put to use. It actually then has to be used. It can't just be theoretically usable. JAY: So we have a lot of useful data people collect. The problem is people never realized lots of them are not usable because of a lack of a label. They have no background, and they're not normalized. So eventually, that is a problem. And even if you have a lot of data, it doesn't mean it is usable. TROND: So then I guess that's how you get to your second layer, which I guess most people just call machine learning, but for you, it's an algorithmic layer, which is where some of the structuring gets done and some of the machines that put an analysis on this, put in place automatic procedures. JAY: And machine learning to me it's like cooking ware like a kitchen. You got a pan fry; you got a steamer; you got the grill. Those are tools to cook the food, the data. Food is like data. Cooking ware is like AI. But it depends on purpose. For example, you want fish. What do you want to eat first? I want soup. There's a difference. Do you want to grill? Do you want to just deep fry? So depending on how you want to eat it, the cooking ware will be selected differently. TROND: Well, and that's super interesting because it's so easy to say, well, all these algorithms and stuff they're out there, and all you have to do is pick up some algorithms. But you're saying, especially in a factory, you can't just pick any tool. You have to really know what the effect would be if you start to...for example, on downtime, right? Because I'm imagining there are very many advanced techniques that could be super advanced, but they are perhaps not the right tool for the job, for the workers that are there. So how does that come into play? Are these sequential steps, by the way? So once you figure out what the data is then, you start to fiddle with your tools. JAY: Well, there are two perspectives; one perspective is predict and prevent. So you predict something is going to happen. You prevent it from happening, number one. Number two, understand the root causes and potential root causes. So that comes down to the visible and invisible perspective. So from the visible world, we know what to measure. For example, if you have high blood pressure, you measure blood pressure every day, but that may not be the reason for high blood pressure. It may be because of your DNA, maybe because of the food you eat, because of lack of exercise, because of many other things, right? TROND: Right. JAY: So if you keep measuring your blood pressure doesn't mean you have no heart attack. Okay, so if you don't understand the reason, measuring blood pressure is not a problem. So I'm saying that you know what you don't know. So we need to find out what you don't know. So the correlation of invisible, I call, visible-invisible. So I will predict, but you also want to know the invisible reason relationship so you can prevent that relationship from happening. So that is really called deep mining those invisibles. So we position ourselves very clearly between visible-invisible. A lot of people just say, "Oh, we know what the problem is." The problem is not a purpose. For example, the factory manufacturing there are several very strong purposes, number one quality, right? Worry-free quality. Number two, your efficiency, how much you produce per dollar. If you say that you have great quality, but I spent $10,000 to make it, it is very expensive. But if you spend $2 to make it, wow, that's great. How did you do it? So quality per dollar is a very different way of judging how good you are. You got A; I spent five days studying. I got A; I spent two hours studying. Now you show the capability difference. TROND: I agree. And then the third factor in your framework seems to be platform. And that's when I think a lot of companies go wrong as well because platform is...at least historically in manufacturing, you pick someone else's platform. You say I'm going to implement something. What's available on the market, and what can I afford, obviously? Or ideally, what's the state of the art? And I'll just do that because everyone seems to be doing that. What does platform mean to you, and what goes into this choice? If you're going to create this platform for industrial AI, what kind of a decision is that? JAY: So DT is data, AT is algorithm, and PT is platform, PT platform. Platform means some common things are used in a shared community. For example, kitchen is a platform. You can cook. I can cook. I can cook Chinese food. I can cook Italian food. I can cook Indian food. Same kitchen but different recipe, different seasoning, but same cooking ware. TROND: Correct. Well, because you have a good kitchen, right? JAY: Yes. TROND: So that's -- JAY: [laughs] TROND: Right? JAY: On the platform, you have the most frequently used tool, not everything. You don't need 100 cooking ware in your kitchen. You probably have ten or even five most daily used. TROND: Regardless of how many different cuisines you try to cook. JAY: Exactly. That's called the AI machine toolkit. So we often work with companies and say, "You don't need a lot of tools, come on. You don't need deep learning. You need a good logistic regression and support-vector machine, and you're done." TROND: Got it. JAY: Yeah, you don't need a big chainsaw to cut small bushes. You don't need it. TROND: Right. And that's a very different perspective from the IT world, where many times you want the biggest tool possible because you want to churn a lot of data fast, and you don't really know what you're looking for sometimes. So I guess the industrial context here really constrains you. It's a constraint-based environment. JAY: Yes. So industry, like I said, the industry we talked about three Ps like I said: problems, purposes, and processes. So normally, problem comes from...the main thing is logistic problems, machine, and factory problems, workforce problems, the quality problems, energy problem, ignition problem, safety problems. So the problem happens every day. That's why in factory world, we call it firefighting. Typically, you firefight every day. TROND: And is that your metaphor for the last part of your framework, which is actually operation? So operation sounds really nice and structured, right? JAY: [chuckles] Yes. TROND: As if that was like, yeah, that's the real thing, process. We got this. But in reality, it feels sometimes, to many who are operating a factory; it's a firefight. JAY: Sometimes the reason lean theme work, Six Sigma, you turn a problem into a process, five Ss process, okay? And fishbone diagram, Pareto chart, and Kaizen before and after. So all the process, SOP, so doesn't matter which year workforce comes in, they just repeat, repeat, repeat, repeat, repeat. So in Toyota, the term used to be called manufacturing is just about the discipline. It's what they said. The Japanese industry manufacturing is about discipline, how you follow a discipline to everyday standard way, sustainable way, consistent way, and then you make good products. This is how the old Toyota was talking about, old one. But today, they don't talk that anymore. Training discipline is only one thing; you need to understand the value of customers. TROND: Right. So there are some new things that have to be added to the lean practices, right? JAY: Yes. TROND: As time goes by. So talk to me then more about the digital element because industrial AI to you, clearly, there's a very clear digital element, but there's so many, many other things there. So I'm trying to summarize your framework. You have these four factors: data, algorithms, platforms, and operations. These four aspects of a system that is the challenge you are dealing with in any factory environment. And some of them have to do with digital these days, and others, I guess, really have to do more with people. So when that all comes together, do you have some examples? I don't know, we talked about Toyota, but I know you've worked with Foxconn and Komatsu or Siemens. Can you give me an example of how this framework of yours now becomes applied in a context? Where do people pick up these different elements, and how do they use them? JAY: There's a matrix thinking. So horizontal thinking is a common thing; you need to have good digital thread including DT, data technology, AT, algorithms or analytics, PT, platform, edge cloud, and the things, and OT operation like scheduling, optimizations, stuff like that. Now, you got verticals, quality vertical, cost vertical, efficiency verticals, safety verticals, emission verticals. So you cannot just talk about general. You got to have focus on verticals. For example, let me give you one example: quality verticals. Quality is I'm the factory manager. I care about quality. Yes, the customer will even care more, so they care. But you have a customer come to your shop once a month to check. You ask them, "Why you come?" "Oh, I need to see how good your production." "How about you don't have to come? You can see my entire quality." "Wow, how do I do that?" So eventually, we develop a stream of quality code, SOQ, Stream Of Quality. So it's not just about the product is good. I can go back to connect all the processes of the quality segment of each station. Connect them together. Just like you got a fish, oh, okay, the fish is great. But I wonder, when the fish came out of water, when the fish was in the truck, how long was it on the road? And how long was it before reaching my physical distribution center and to my home? So if I have a sensor, I can tell you all the temperature history inside the box. So when you get your fish, you take a look; oh, from the moment the fish came out of the boat until it reached my home, the temperature remained almost constant. Wow. Now you are worry-free. It's just one thing. So you connect together. So that's why we call SOQ, Stream Of Quality, like a river connected. So by the time a customer gets a quality product, they can trace back and say, "Wow, good. How about if I let you see it before you come? How about you don't come?" I say, "Oh, you know what? I like it." That's what this type of manufacturing is about. It just doesn't make you happy. You have to make the customer happy, worry-free. MID-ROLL AD: In the new book from Wiley, Augmented Lean: A Human-Centric Framework for Managing Frontline Operations, serial startup founder Dr. Natan Linder and futurist podcaster Dr. Trond Arne Undheim deliver an urgent and incisive exploration of when, how, and why to augment your workforce with technology, and how to do it in a way that scales, maintains innovation, and allows the organization to thrive. The key thing is to prioritize humans over machines. Here's what Klaus Schwab, Executive Chairman of the World Economic Forum, says about the book: "Augmented Lean is an important puzzle piece in the fourth industrial revolution." Find out more on www.augmentedlean.com and pick up the book in a bookstore near you. TROND: So, Jay, you took the words out of my mouth because I wanted to talk about the future. I'm imagining when you say worry-free, I mean, you're talking about a soon-to-be state of manufacturing. Or are you literally saying there are some factories, some of the excellence factories where you've won awards in the World Economic Forum or other places that are working towards this worry-free manufacturing, and to some extent, they have achieved it? Well, elaborate for me a little bit about the future outlook of manufacturing and especially this people issue because you know that I'm engaged...The podcast is called Augmented Podcast. I'm engaged in this debate about automation. Well, is there a discrepancy between automation and augmentation? And to what extent is this about people running the system? Or is it the machines that we should optimize to run all the system? For you, it's all about worry-free. First of all, just answer this question, is worry-free a future ideal, or is it actually here today if you just do the right things? JAY: Well, first of all, worry-free is our mindset where the level of satisfaction should be, right? TROND: Yep. JAY: So to make manufacturing happen is not about how to make good quality, how to make people physically have less worry, how to make customers less worry is what is. But the reason we have a problem with workforce today, I mean, we have a hard time to hire not just highly skilled workers but even regular workforce. Because for some reason, not just U.S., it seems everywhere right now has similar problems. People have more options these days to select other living means. They could be an Uber driver. [laughs] They could be...I don't know. So there are many options. You don't have to just go to the factory to make earnings. They can have a car and drive around Uber and Lyft or whatever. They can deliver the food and whatever. So they can do many other things. And so today, you want to make workforce work environment more attractive. You have to make sure that they understand, oh, this is something they can learn; they can grow. They are fulfilled because the environment gives them a lot of empowerment. The vibe, the environment gives them a wow, especially young people; when you attract them from college, they'd like a wow kind of environment, not just ooh, okay. [laughs] TROND: Yeah. Well, it's interesting you're saying this. I mean, we actually have a lack of workers. So it's not just we want to make factories full of machines; it's actually the machines are actually needed just because there are no workers to fill these jobs. But you're looking into a future where you do think that manufacturing is and will be an attractive place going forward. That seems to be that you have a positive vision of the future we're going into. You think this is attractive. It's interesting for workers. JAY: Yeah. See, I often say that there are some common horizontal we have to use all the day. Vertical is the purpose, quality. I talked about vertical quality first, quality. But what are the horizontal common? I go A, B, C, D, E, F. What's A? AI. B is big data. C is cyber and cloud. D is digital or digital twin, whatever. E is environment ecosystem and emission reduction. What's F? Very important, fun. [laughs] If you miss that piece, who wants to work for a place there's no fun? You tell me would you work for...you and I, we're talking now because it's fun. You talk to people and different perspectives. I talk to you, and I say, wow, you've built some humongous network here in the physical...the future of digital, not just professional space but also social space but also the physical space. So, again, the fun things inspire people, right? TROND: They do. So talking about inspiring people then, Jay, if you were to paint a picture of this future, I guess, we have talked just now about workers and how if you do it right, it's going to be really attractive workplaces in manufacturing. How about for, I guess, one type of worker, these knowledge workers more generally? Or, in fact, is there a possibility that you see that not just is it going to be a fun place to be for great, many workers, but it's actually going to be an exciting knowledge workplace again? Which arguably, industrialization has gone through many stages. And being in a factory wasn't always all that rosy, but it was certainly financially rewarding for many. And it has had an enormous career progression for others who are able to find ways to exploit this system to their benefit. How do you see that going forward? Is there a scope, is there a world in which factory work can or perhaps in an even new way become truly knowledge work where all of these industrial AI factors, the A to the Fs, produce fun, but they produce lasting progression, and career satisfaction, empowerment, all these buzzwords that everybody in the workplace wants and perhaps deserves? JAY: That's how we look at the future workforce is not just about the work but also the knowledge force. So basically, the difference is that people come in, and they become seasoned engineers, experienced engineers. And they retire, and the wisdom carries with them. Sometimes you have documentation, Excel sheet, PPT in the server, but nobody even looks at it. That's what today's worry is. So now what you want is living knowledge, living intelligence. The ownership is very important. For example, I'm a worker. I develop AI, not just the computer software to help the machine but also help me. I can augment the intelligence. I will augment it. When I make the product happen, the inspection station they check and just tell me pass or no pass. They also tell me the quality, 98, 97, but you pass. And then you get your score. You got a 70, 80, 90, but you got an A. 99, you got an A, 91, you got an A, 92. So what exactly does A mean? So, therefore, I give you a reason, oh, this is something. Then I learn. Okay, I can contribute. I can use voice. I can use my opinion to augment that no, labeled. So next time people work, oh, I got 97. And so the reason is the features need to be maintained, to be changed, and the system needs to be whatever. So eventually, you have a human contribute. The whole process could be consisting of 5 experts, 7, 10, 20, eventually owned by 20 people. That legacy continues. And you, as a worker, you feel like you're part of the team, leave a legacy for the next generation. So eventually, it's augmented intelligence. The third level will be actual implementation. So AI is not about artificial intelligence; it is about actual implementation. So people physically can implement things in a way they can make data to decisions. So their decision mean I want to make an adjustment. I want to find out how much I should adjust. Physically, I can see the gap. I can input the adjustment level. The system will tell me physically how could I improve 5%. Wow, that's good. I made a 5% improvement. Your boss also knows. And your paycheck got the $150 increase this month. Why? Because my contribution to the process quality improved, so I got the bonus. That's real-world feedback. TROND: Let me ask you one last question about how this is going to play out; I mean, in terms of how the skilling of workers is going to allow this kind of process. A lot of people are telling me about the ambitions that I'm describing...and some of the guests on the podcasts and also the Tulip software platform, the owner of this podcast, that it is sometimes optimistic to think that a lot of the training can just be embedded in the work process. That is obviously an ideal. But in America, for example, there is this idea that, well, you are either a trained worker or an educated worker, or you are an uneducated worker. And then yes, you can learn some things on the job. But there are limits to how much you can learn directly on the job. You have to be pulled out, and you have to do training and get competencies. As you're looking into the future, are there these two tracks? So you either get yourself a short or long college degree, and then you move in, and then you move faster. Or you are in the factory, and then if you then start to want to learn things, you have to pull yourself out and take courses, courses, courses and then go in? Or is it possible through these AI-enabled training systems to get so much real-time feedback that a reasonably intelligent person actually never has to be pulled out of work and actually they can learn on the job truly advanced things? So because there are two really, really different futures here, one, you have to scale up an educational system. And, two, you have to scale up more of a real-time learning system. And it seems to me that they're actually discrepant paths. JAY: Sure. To me, I have a framework in my book. I call it the four P structure, four P. First P is principle-based. For example, in Six Sigma, in lean manufacturing, there's some basic stuff you have to study, basic stuff like very simple fishbone diagram. You have to understand those things. You can learn by yourself what that is. You can take a very basic introduction course. So we can learn and give you a module. You can learn yourself or by a group, principle-based. The second thing is practice-based. Basically, we will prepare data for you. We will teach you how to use a tool, and you will do it together as a team or as individual, and you present results by using data I give to you, the tool I give to you. And it's all, yeah, my team A presented. Oh, they look interesting. And group B presented, so we are learning from each other. Then after the group learning is finished, you go back to your team in the real world. You create a project called project-based learning. You take a tool you learn. You take the knowledge you learn and to find a project like a Six Sigma project you do by yourself. You formulate. And then you come back to the class maybe a few weeks later, present with a real-world project based on the boss' approval. So after that, you've got maybe a black belt but with the last piece professional. Then you start teaching other people to repeat the first 3ps. You become master black belt. So we're not reinventing a new term. It really is about a similar concept like lean but more digital space. Lean is about personal experience, and digital is about the data experience is what's the big difference. TROND: But either way, it is a big difference whether you have to rely on technological experts, or you can do a lot of these things through training and can get to a level of aptitude that you can read the signals at least from the system and implement small changes, perhaps not the big changes but you can at least read the system. And whether they're low-code or no-code, you can at least then through learning frameworks, you can advance, and you can improve in not just your own work day, but you can probably in groups, and feedbacks, and stuff you can bring the whole team and the factory forward perhaps without relying only on these external types of expertise that are actually so costly because they take you away. So per definition, you run into this; I mean, certainly isn't worry-free because there is an interruption in the process. Well, look, this is fascinating. Any last thoughts? It seems to me that there are so many more ways we can dig deeper on your experience in any of these industrial contexts or even going deeper in each of the frameworks. Is there a short way to encapsulate industrial AI that you can leave us with just so people can really understand? JAY: Sure. TROND: It's such a fundamental thing, AI, and people have different ideas about that, and industry people have something in their head. And now you have combined them in a unique way. Just give us one sentence: what is industrial AI? What should people leave this podcast with? JAY: AI is a cognitive science, but industrial AI is a systematic discipline is one sentence. So that means people have domain knowledge. Now we have to create data to represent our domain then have the discipline to solve the domain problems. Usually, with domain knowledge, we try with our experience, and you and I know; that's it. But we have no data coming out. But if I have domain become data and data become discipline, then other people can repeat our success even our mistake; they understand why. So eventually, domain, data, discipline, 3 Ds together, you can make a good decision, sustainable and long-lasting. TROND: Jay, this has been so instructive. I thank you for spending this time with me. And it's a little bit of a never-ending process. JAY: [laughs] TROND: Industry is not something that you can learn it and then...because also the domain changes and what you're doing and what you're producing changes as well. So it's a lifelong -- JAY: It's rewarding. TROND: Rewarding but lifelong quest. JAY: Yeah. Well, thank you for the opportunity to share, to discuss. Thank you. TROND: It's a great pleasure. You have just listened to another episode of the Augmented Podcast with host Trond Arne Undheim. The topic was Industrial AI. And our guest was Professor Jay Lee from University of Cincinnati. In this conversation, we talked about how AI in industry needs to work every time and what that means. My takeaway is that industrial AI is a breakthrough that will take a while to mature. It implies discipline, not just algorithms. In fact, it entails a systems architecture consisting of data, algorithm, platform, and operation. Thanks for listening. If you liked the show, subscribe at augmentedpodcast.co or in your preferred podcast player, and rate us with five stars. If you liked this episode, you might also like Episode 81: From Predictive to Diagnostic Manufacturing Augmentation. Hopefully, you'll find something awesome in these or in other episodes, and if so, do let us know by messaging us. We would love to share your thoughts with other listeners. The Augmented Podcast is created in association with Tulip, the frontline operation platform that connects the people, machines, devices, and systems used in a production or logistics process in a physical location. Tulip is democratizing technology and is empowering those closest to operations to solve problems. Tulip is also hiring. You can find Tulip at tulip.co. Please share this show with colleagues who care about where industry and especially where industrial tech is heading. To find us on social media is easy; we are Augmented Pod on LinkedIn and Twitter and Augmented Podcast on Facebook and YouTube. Augmented — industrial conversations that matter. See you next time.Special Guest: Jay Lee.