Episode 88: The Future of Digital in Manufacturing
Augmented Ops - Un pódcast de Tulip - Miercoles
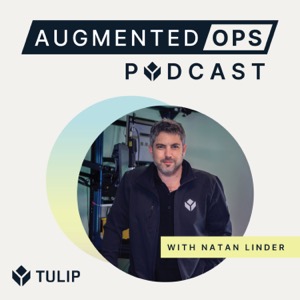
Categorías:
Augmented reveals the stories behind the new era of industrial operations, where technology will restore the agility of frontline workers. In episode 21 of the podcast @AugmentedPod, the topic is: "The Future of Digital in Manufacturing." Our guest is Çağlayan Arkan, VP of Manufacturing Industry at Microsoft (@Caglayan_Arkan). In this conversation, we talk about where manufacturing has been in the past, why manufacturing has been lacking a sense of urgency in the sense of industry 4.0 but how everything we know about manufacturing has changed. We also discuss workforce transformation, democratizing operational technology, and the future of industrial innovation.After listening to this episode, check out Microsoft's manufacturing approach as well as Çağlayan Arkan's social media profile:Microsoft Cloud for Manufacturing: https://www.microsoft.com/en-us/industry/manufacturing/microsoft-cloud-for-manufacturing Çağlayan Arkan: LinkedIn, Blog: https://aka.ms/CaglayanArkanBlogTrond's takeaway: The future of digital in manufacturing is enormously impactful. Yet, even deep digitalization will not make workers obsolete. Rather, the challenge seems to be achieving a dramatic workforce transformation which also entails empowerment, upskilling, and autonomy through augmentation of frontline operations.Thanks for listening. If you liked the show, subscribe at Augmentedpodcast.co or in your preferred podcast player, and rate us with five stars. If you liked this episode, you might also like episode 9, The Fourth Industrial Revolution post-COVID-19, episode 4, A Renaissance in Manufacturing or Episode 20, The Digitalization of Körber.Augmented--industrial conversations. Transcript: Augmented reveals the stories behind a new era of industrial operations, where technology will restore the agility of frontline workers. In Episode 21 of the podcast, the topic is The Future of Digital in Manufacturing. Our guest is Çağlayan Arkan, VP of Manufacturing Industry at Microsoft. In this conversation, we talk about where manufacturing has been in the past, why manufacturing has been lacking a sense of urgency in the sense of industry 4.0, but how everything we know about manufacturing has changed. We also discuss workforce transformation, democratizing operational technology, and the future of industrial innovation. Augmented is a podcast for leaders hosted by futurist, Trond Arne Undheim, presented by Tulip.co, the frontline operations platform, and associated with MFG.works, the manufacturing upskilling community launched at the World Economic Forum. Each episode dives deep into a contemporary topic of concern across the industry and airs at 9:00 a.m. U.S. Eastern Time every Wednesday. Augmented - the industry 4.0 podcast. Çağlayan, how are you today? ÇAĞLAYAN: I am very well. Great to be here. Thank you. TROND: So I am alerted to the fact that you're an outdoor person. And I wanted to cover that just because a technology discussion in manufacturing is not complete without a little bit of personality. And I think you said you are a backcountry skier. I was curious about this. ÇAĞLAYAN: I am. Skiing is my passion, one of them, but probably the one that makes me happiest, the one that I love the most. I like ski touring, and I like skiing the backcountry, the off-piste. I like climbing. I'm a very physical person. And on a similar note, I also am a cyclist. I'm a sailor, a windsurfer. I just love being out, and I love the wind on my face. TROND: So at some point in the future, when the pandemic is over and behind us, I think my next podcast with you we will simply go for a hike. ÇAĞLAYAN: Well, let's do it. But doing it with me has the following potential downside for you. The other piece of my outdoors work, or kind of world, if you will, is that I love miserable weather. I'm a winter person. I love my rain, my cold, my wind. [laughs] And people typically, even if they categorize themselves as outsiders, like outdoor people, they will just love fair weather, I don't. I'm not that person. I don't like the sun on my face. I don't like a lot of people out. I like trails to myself. I like mountains to myself. [laughs] If you're up for it, we'll do it together. TROND: Well, this is probably something you didn't realize. But I grew up in Norway, and there are no people. And we have plenty of bad weather. So admittedly, I don't live in Norway, so that could give you a clue. [laughter] But there is something there. ÇAĞLAYAN: All right, we're on. We're on. TROND: Yeah, we're on. Okay, so having settled that, I wanted to ask you this question. So we're going to talk about, I guess, the future and the current state, present state of manufacturing. But where has manufacturing been in the past? And by the way, when you think past, how far do you go back? I mean, is this just pre-COVID? Because I've heard you talk a little bit about manufacturing traditionally, and I want you to just give us a quick sense of where you think the industry was just a few moments ago. ÇAĞLAYAN: You started personally. Let me personalize manufacturing for me. I'm an industrial engineer with an MBA. And so, my whole education was in plants in the manufacturing environment. And I studied from operations research to metallurgical engineering, to electrical engineering, to construction, to electrical. You just name it. And so that has been something that I really really liked, the system's thinking, the optimization. I've done a lot in OR back in the day, linear and multiple. So maybe too much detail for now. But where is manufacturing? Manufacturing has been mostly manual siloed with a separation between information technology and the data estate that that brings to the table and operations technology that that brings to the table. Technology has never really been, particularly from an IT standpoint, top of mind. Digital transformation has not really been a sense of urgency in manufacturing because things worked. Yet people at the shop floor and things were working until the pandemic hit. So pandemic question, slap on the face for manufacturers. Business continuity none. You can't send people to the shop floor. You cannot operate. You don't see your inventory. You can't see your suppliers. You don't even know whether they're surviving or not, financially or otherwise. So it was a huge, huge, huge problem. But the silver lining of all of this is now there's acceleration into the transformation of manufacturing. Look, why is manufacturing important? Let's spend a minute on that. Manufacturing, unlike many other industries (And I kind of make fun of my peer industry leaders at Microsoft as well.), manufacturing is very real. Manufacturing creates employment. Manufacturing creates growth, builds the economy, builds capacity. Manufacturing is about innovation. Manufacturing is about competitiveness. So it is core to populations, countries. It's core to politicians, to business leaders, and it's just phenomenal. And so if you do things right in manufacturing, things work, including climate change, and sustainability, and a lot of other stuff. And if you do things wrong, you could see a lot of damage done. It collapses economies. It collapses, grids and stops, and creates a lot of disruption. So it is very real. And so I'm sorry I'm providing a long answer, but you can tell I'm passionate about it. It's very personal for me. But by and large, I'm actually excited about where we are. We are at an inflection point. And we'll see a lot of acceleration coming out of the pandemic, the crisis. And stuff we're working on is actually to ensure business continuity and resiliency. Those are the things that are the conversations going forward. TROND: Çağlayan, you took me in an interesting direction. I was just thinking as you were speaking, right before we go to the inflection, it's actually not just a little bit surprising but actually quite surprising that there haven't been any reported massive disruptions due to the pandemic. If you think about all of these mission-critical systems that we have around the world, in every manufacturing-related industry, how do you explain because, as you were saying, historically...and some of these silos are sort of still there, although obviously, we are at this inflection point so somehow already transitioned. But how do you explain that we haven't had more horror stories? And by horror stories, I guess I mean operations completely collapsing, or I guess grids falling apart, or that one manual worker couldn't go in. So X happened that they had never, never thought about. Why haven't we heard anything like that? Are those stories going to come out, do you think, or did nothing seriously happen? ÇAĞLAYAN: Well, it happened. I know for a fact because once this started, I started calling down on my customers, like, "How are you doing? What do you need?" For one, I think that from a table stakes standpoint, we've seen massive teams deployment because people wanted to communicate. They wanted continuity in terms of being able to talk to one another, being able to work, and then work from home, of course, because they couldn't go to their plants or to their offices. So there was a lot of pain. There was a lot of disruption. I talked to some of my customers, and they were like, billions of dollars are tied in inventory, and we have no idea where that sits. Again, they're disconnected from suppliers as well as their customers, and so there was disruption. But luckily, we've had some leaders actually having foreseen what is to come, or they were disruptors or at least early adopters. And they have taken pre-COVID pre-crisis steps for digital transformation. And I love my examples and partnerships where Erickson had started work pre-COVID in terms of digital manufacturing, Outokumpu, a leader in steel manufacturing, significant progress including during the pandemic, Airbus, Unilever. I mean, those are leading examples, only some of them. But you look at the World Economic Forum Global Lighthouse Network; there are so many lighthouse factories that are just like literally lighthouses for people to look at and look up to. That work started years ago. So there are some extremely encouraging examples. There are some very, very dark stories in terms of complete stoppage and horror stories. But by large, we are at a good place in terms of we understand the issues and we understand how to deal with them. And I think most importantly, that notion of time to value is accelerated in manufacturing. And we're coming from prohibitively expensive, I mean, we're talking hundreds of millions of dollars of IT projects that never end to now negligible cost and like 10-12 weeks, a couple of months, and then you stand up a digital factory capability. You have visibility into your supply chain by standing up a control tower. And then, in the case of Airbus or Alstom, you can have your 2,000 engineers still keep doing design and engineering work from home; examples go on. But we understand the issues. We have a very quick ability to build capability, to show that stuff works and you can operate remotely, et cetera, et cetera. TROND: But would you say that this is the definite end to, I guess what you were alluding to is kind of this pilot purgatory? Is COVID the definite end to pilot purgatory? Or is it just that this particular situation was so serious that everybody kind of scrambled, and most of them got it right? Or would you say that...I guess possibly because once you have made this transition, that is the hard work. Do you think that these pilots that everyone was waiting for will that problem disappear because people have learned that this is not the way to introduce technology? You sort of learned it the hard way. ÇAĞLAYAN: Oh, well, my view is if you take a step back, Trond, here's how I see it. One hundred years ago, we were by and large an agricultural society, and we had like 50% of the workforce in agriculture. Today we are by and large an industrial society. And we have like 2% of the workforce in agriculture, and we brought everyone along in terms of The Industrial Age. Today we are at the next junction; some call it industry 4.0, some call it other names. But we as a society assume...like humanity, we're moving from industrial to digital. So that's the higher order. Now, what's the role of the pandemic in this? I think it's that of acceleration. So in any major shift, there are behaviors and categories of actors or players. There are the disruptors. There are those who go and make a market, build a trend. And we have seen those, and we're still seeing them. They are the early adopters. We talked about some of them as well. And then there's going to be the slower adopters and the laggards. And then some of the laggards will not see the light of day or will not maybe exist after we transition to the new reality, new realm, or that notion of digital society. So what I'm saying is it was going to happen, those pilots or people's way, like, slow adopters' way of touching it, putting their toes in the water. For some, it's proving value and acceleration. Pandemic, again, that kind of disruption is going to accelerate and bring more to the table. But it certainly has a role to play. But the higher-level order is we are moving to a very, very different reality for manufacturers and supply chains and even as a society. TROND: Super interesting. Çağlayan, I've heard you talk earlier. And I guess we talked a little bit in the prep about whether this is a different wave of technology because I know you have some views on the democratization of basically operational technology because there are different waves of technology in manufacturing. And traditionally, like you said, the industry has been siloed. But one of the reasons the industry was siloed is that the technology then also turned into silos, arguably. And what is it about the technology these days? Is it getting simpler? Are you, for instance, in Microsoft spending more time on user interfaces than you were before? Or I guess even the introduction of your company so deeply into manufacturing is in and of itself a bit of a novelty. The tech players that weren't specialists are now going deep, deep into industry segments. Give me a sense of why this is happening. And what exactly is this democratization? Gartner calls it citizen developers. ÇAĞLAYAN: Yeah, that's one aspect of it. The way I see it is, very shortly, technology now works. TROND: [laughs] ÇAĞLAYAN: Honestly, I don't know, like five years ago, it just didn't. It was so hard for implementations, for integration, et cetera. It now works. There's virtually nothing technology cannot deliver today. It's up to the leader's vision, leader's ability to execute, and magic happens. There's so much at play right now, that's one. Secondly, technology is the business right now. I mean, technology was isolated. Trond, you will remember those days not too distant past. We had our own language. The CIO, it's like they were from Mars in the organization. [laughter] And they were not mainstream as an executive in the company. Company did their work, and CIO did stuff that nobody really understood. Now, technology is the business. I mean, if you look at any research, you will see that the mainstream business leader, whether it's the CMO, the Chief, Marketing Officer, Chief Digital Officer, Chief Financial Officer, whatever those may be, they're making more technology decisions and have bigger technology budgets than the technology people themselves. So that's the other piece that business is technology. Technology is business. The third piece is that the siloed nature of not only manufacturing, so many different industries, was because it was an application-led view into enterprises or into business. Now, it's data-driven work. And so data dictates everything, and data is actually end to end. So to the extent that you have a data architecture, enterprise-level data architecture, and a system-level approach to things, it's a completely different world. And to bring those three together as a business, you have to forget more than you remember. And then you have to reinvent yourself. And if you do that, everybody knows cliché examples here, but then you find yourself as a completely different company or services company or actually at the risk of being disrupted by competition in ways that were not thought of or unprecedented. So that's what's happening. So what we like to approach this whole kind of...I like to call this opportunity. It's a major opportunity. It's a huge inflection point. It's all about reinventing your business. None of that is about technology. Technology is a tool. It's a powerful tool. It's a tool that works. It's very capable. But it's about the business outcomes. Because we said, you have to reinvent your entire enterprise, starting from your culture, how you operate, your value proposition, all of that. It is where you start should be dictated by which outcome is most important for you, or the highest value for you, or the most burning for you. Whatever your drivers are, focus on the outcome. Go back to work to find the relevant data for it and get to that in weeks, literally seriously in weeks and get to the next outcome, the next outcome. And don't forget the people and culture. It's all about the people piece, and we can talk about that later. I think we should. But those are the things that I will say to your technology question. TROND: That's great. ÇAĞLAYAN: Focus on data, lead with culture, and always major prioritizations on the outcomes you want to drive. TROND: You said lead with culture, but it's not just company culture, I guess. It's the whole nature of the skills that are now needed in this new workplace. A lot of people are saying that that is changing and that the workforce needs are changing. So you initially said well, technology now works. So that's true, but what are the skills that then are needed? So okay, technology is easier. But what are some of the tasks that are, I guess, less relevant because of this influx of call it industry 4.0 type technologies? And what are some of the skills that are more relevant? And the frontline worker of the future, what should they be focused on? And your clients, what are they starting to teach their workforce? ÇAĞLAYAN: Great question. I will say at the highest level, Trond, it is a data-driven culture. I mean, in manufacturing, maybe other businesses and industries as well, we operate on the basis of past successes, habits. This has been delivering for me. This has been working for me, et cetera, or experience. You kind of listen to stuff. You kind of watch stuff. You anticipate stuff. And you're like, I've been doing this for 25 years. None of this has anything to do with data because, again, we established we were using less than 1% of our data, at least in manufacturing. Now the biggest cultural change is data-driven. And then once you go to data telling you what to do, data giving you predictions, data giving you systems of intelligence like the insights in terms of what to do, and when to do it, and how to do it, et cetera, then that dictates actually two things. Again, I'm trying to come down to it in terms of a hierarchy. Manufacturing had a skills gap, has a bigger skills gap in the face of digital. And we're not an attractive industry. The young generation does not see career opportunities in manufacturing. Actually, manufacturing is fantastic. It's real; it's innovative. So we have to change that, and so we're working on it. And secondly, the existing jobs, even if they may still be the most important jobs in manufacturing, those people have to learn new skills in terms of doing their jobs using technology. Let's see now a couple of examples. You talked about the frontline workers, first-line workers, or just shopfloor, the very people who get the job done. They typically did not use any technology. They were all mostly manual, what we called HMI, like Human-Machine interfaces, old, very, very, antique equipment, if you will, blue screens. I think anyone who's close to manufacturing will know that we used a lot of paper, et cetera. Today's frontline worker is actually acting on data, acting on predictions, double-clicking under the modern interface, and responding to traffic lights, responding to alerts. You got to be able to do those, wearing augmented or virtual reality devices. We call it mixed reality with the unique technology that we have in terms of HoloLens in our entire mixed reality platform. But you come to a job, and then you don't need to learn to do the job. You just wear your HoloLens. And the mixed reality platform will actually teach you how to do it with your two hands-free. If you're in the field service, someone at the back office, remote connections, or remote assist capabilities can actually guide you through as to how to deal with that; I don't know, grid asset, extruder, or packaging line because they know how to and you don't need to. And then this is the way you learn how to do stuff. So I guess the gist of it is some jobs will no longer exist. Most of the repetitive low-value-added jobs can be automated, robots, artificial intelligence, and other means in terms of process automation, et cetera. Most of the jobs, if not all of the jobs, will be rescaled in terms of technology. And at the highest level, probably 75 million jobs will go away. Again, this is a World Economic Forum study. One hundred thirty-five million new jobs will be created. What are those jobs? Data jobs, software jobs. And then how you do your design and engineering, you have to be able to understand AI-led generative design, additive manufacturing, 3D printing to be able to be successful. And so, all of that is a call to action for universities, policymakers, corporate learning officers, for all of us, and calls for partnerships to lean in. And again, I used agricultural example. Bring everyone along from the Industrial Age to the digital age. TROND: It's a fascinating challenge, and it's a big one. I was just curious; there's a lot of talk about middle jobs meaning jobs that are somewhere between more than high school but less than traditional college. But then you also have an echelon above that, of course, which traditionally certainly Microsoft was hiring into, which is more high-level cognitive jobs which required bachelors, and masters, and PhDs traditionally in computer programming. But I'm guessing now certainly in your field in sort of hybrid engineering studies where engineering plus IT. The middle jobs is a big challenge, even just from an operational point of view. It's hard to educate a billion people worldwide or whatever it is that we have to do continuously to keep the lights up. How is all that going to happen? And what sort of effort does this require? Can we use the existing institutions we have to do this? Or do you foresee that it's going to be a lot more on-the-job type of training in digital training? ÇAĞLAYAN: I'll say all of the above in the following ways; for one, we're already working with Purdue, University of Wisconsin, and many, many universities and education institutions. So for one, manufacturing-related jobs were kind of graduate jobs. We're trying to bring the curriculum to undergrad, if not high school, so there's that. So vocational training, et cetera, all of this is important. Secondly, we partner with the National Association of Manufacturers, MxD, Sesame, obviously Tulip, and many others in terms of call to action and doing institutionalizing, programatize, very, very important for all of that. Thirdly, I deliberately talked about corporate learning officers because a lot of people, tens if not hundreds of thousands of people in large corporations, actually had to learn new skills. And it is happening as we speak in multiple ways in many, many, many, many leading enterprises. But it's a huge part of the whole equation. And then, I talked about the World Economic Forum and the Global Lighthouse Network. Programs like that actually bring it to everyone's attention in terms of what is possible, and how it works, and how some leading institutions deal with it, which brings me to this notion of what I like to call art of possible. I think leadership at large, political leaders, enterprise leaders, any institution, education, leadership at large has to understand what I call the art of possible, and that is how technology has already transformed everyone's lives. And what is that leaders need to do differently? Starting from communication, setting new standards, to building the new curriculum, to encouraging everyone, bringing everyone along, and all the rest of it from cultural change to change management and defining the new normal. But by and large, just bringing everyone along. And so that is really, really important that we start that education and understanding with the leadership because it's all about leadership. It's all about them having the right vision and being able to execute to that. TROND: What is the role of actors such as startups? You mentioned Tulip. What are startups' role in the emerging manufacturing and frontline operations ecosystem? Tulip thinks of itself a little wider than manufacturing. But what is it that startups can do? Because clearly, this is a game, technology overall, and also industries. It's an industrial game. Industrial companies are massive traditionally. So the juxtaposition traditionally in the old world would be between the industrial conglomerates and then the SMEs. And the game was to get the SMEs to be useful providers and suppliers into the supply chain ecosystem was an educational challenge. But you now have startups somewhere in this picture as well. Can you address how you think these startups function in the ecosystem going forward? ÇAĞLAYAN: Yeah, I think the example that I would use is startups are like Tesla for automotive, Airbnb for hospitality. They're the disruptors. They have zero legacy. And so we're talking major change, major transformation. What happens in change? Lots of the legacy will drag their feet. They will want to protect status quo. They'll be slower. What startups do is they teach you the new normal. They teach you the art of possible, and they go on and do it. This is how you carry from years of implementation time to weeks. This is how you go from hundreds of millions of dollars to pennies and cents. And so Tulip and many, many others that I'm so excited to work together with, define the new normal. They make it happen. They go and make stuff. And actually, they are the ones who bring what I call art of possible to life. Let's take Tulip's example. Again, they go into the shop floor. And they look at that low-code/no-code citizen developers, a term that you used in this very conversation. And then they bring it to life in the context of manufacturing operations. And so suddenly, the human-machine interfaces are modernized. The legacy-heavy applications that do not necessarily connect the enterprise have changed, and there's a new workflow in place. And people just act on data and intelligence. The job is much easier to do, et cetera, and then you can build on it. And so what they do is just extremely important, actually much bigger than their sizes or the number of people that they employ. The role that they play is actually what's going to change economies. And this is one reason why we embrace and work very, very closely with the likes of Tulip at Microsoft through multiple, multiple tools and investments that we have from Microsoft for Startups to M12 and to many others. TROND: Yes, I understand. That's fantastic. However, it does remain the case that right now, you are a gorilla in the big space, and you do have a privileged position to analyze what you think is happening. So if you use that futurist hat that you have from your vantage point of a large player that does work with everyone, I guess, where is this now heading? You said it's a disruptive time. It's an inflection point. You were using big, revolutionary words. We're talking about industry revolutions. There's also some uncertainty, and we have been dealing with resilience issues. But you pointed out simplicity has improved. Where is all this taking us, all of these bits and pieces altogether? Where is the manufacturing industry heading? ÇAĞLAYAN: Manufacturing is very complex, and it's actually not one industry. So many industries are manufacturers. So let's kind of break it down and simplify to maybe customer-facing systems, sales, services, et cetera, design, and engineering making stuff which is really manufacturing, supply chains, and then maybe you look at people. In the customer systems, particularly the pandemic, taught us that online sales and delivery, omnichannel strategies, profit optimization, pricing, contact lifecycle management, all of that is here to stay. Connected field services or field services at large is going to be changed forever. Again, we talked about mixed reality, remote assistant, remote capabilities, all of that. So that is where that is headed. In terms of the design and engineering piece, we talked about AI-led generative design, where AI engines actually design stuff like mother nature. They don't have corners. They're not straight lines. So the existing manufacturing paradigms like welding, and bending, and et cetera, can go away, and 3D printing actually is very revolutionary in that it's the only way to actually make the stuff that is designed by AI engines which is faster, stronger, lighter, cheaper, et cetera. But again, you can only build them with the new 3D or additive paradigms, and so there's that. And obviously, from design and engineering, that whole design supply chain is moving to a virtual environment so that you do not have to send designs in paper when it comes to like...You look at Boeing, and they have like six million suppliers. You look at Rolls Royce, the same deal. And then what they do now is they send electronic drawings. You can validate. You can verify the source is correct. You can just keep building in the virtual environment, and you can run simulations and tests. I can go on and on, but that is completely disrupted and changed forever. Manufacturing as we know it is moving to...some call it lights-out manufacturing. But this whole remote capability being able to...business continuity, people at the shop floor being able to remotely operate, manage and monitor your assets, get predictions on them, actually have predictions visibility into your suppliers and be connected to their environment. Digital twins and digital threads are actually huge enablers from that perspective. So this whole kind of lights-out manufacturing conversation can happen. Again, technology is capable of delivering it. You have to optimize or rationalize for your own enterprise. Supply chains, completely moving to an autonomous and sustainable fashion. And then finally, at the highest level, what we're seeing perhaps the largest opportunity is go from your...even your own enterprise was siloed. Let alone your enterprise, go and reinvent the whole value chain that you operate in. We tend to think about industries, but actually, value chains are made up of multiple adjacent industries. Look at food; it starts with perhaps the farmer, but the farm equipment manufacturer, the likes of John Deere, Mahindra, et cetera, do play a huge role. There's a lot of data there. Then you look at warehouses, then you look at mills, and processors, and packagers, and shippers, and then you go all the way to retail. I've talked about seven different industries. The notion of I call it lead with opportunity as opposed to leading with risks. Share your data for the greater good. New value creation at the value chain level we haven't even begun starting that journey, really. And so, just some of the examples of how everything we know is already disrupted. Again, do all the leaders know, the world leaders know how to deal with it or where to take their enterprises, their people, their cultures, their businesses? And so that's kind of the conversation. TROND: Indeed it is. Disruption at the value chain level that seems to be at the core. And then I guess my last question for you really is to take this back to the human being because I know you think that fundamentally, this is not really about the technologies or even just the various industries at the center, and maintaining and constructing is the human being. The augmented human capabilities that these new structures and technologies enable, what does that look like? I mean, if you think augmented reality and mixed reality, HoloLens is like a beginning of that vision. But it seems like we're arguably going from a day where the idea was automate, but you have a vision of more augmenting, meaning you're supplementing the human as opposed to replacing them. How do you see the human being in this picture? What is going to be the role of the human worker? ÇAĞLAYAN: Well, it's going to be a combination of vision and maybe aspiration. But I'll say augmented society first because of diversity and inclusion. Let's start there. Let's bring everyone along. Let's not leave one person behind, wherever they may be, whatever background. Let's bring everyone along. And as a society, let's elevate everyone. Let's make everything accessible, technology, and data, and education, and health, and water, and safe food, all of that accessible to everyone. The new set of paradigms actually might create value at such a level in which we can give people more free time, more fulfillment, provide better work-life balance, provide other means of seeking reason and purpose in life and communicate and work together at very, very different levels. And so all of that is just, again, I think this whole kind of leader, art of possible, and what technology is capable of today. If we put the people in the center and go from there, I think we can remember these days as some of the best kind of inflection points in history. TROND: Wow, that's a great way to end. I thank you so much. This was a whirlwind of observations. [laughs] Thank you very much. ÇAĞLAYAN: Thank you. TROND: You have just listened to Episode 21 of the Augmented Podcast with host Trond Arne Undheim. The topic was The Future of Digital in Manufacturing, and our guest was Çağlayan Arkan, VP of Manufacturing Industry at Microsoft. In this conversation, we talked about where manufacturing has been in the past, workforce transformation, democratizing operational technology, and the future of industrial innovation. My takeaway is that the future of digital in manufacturing is enormously impactful, yet even deep digitalization will not make workers obsolete. Rather, the challenge seems to be achieving a dramatic workforce transformation which also entails empowerment, upskilling, and autonomy through augmentation of frontline operations. Thanks for listening. If you liked the show, subscribe at augmentedpodcast.co or in your preferred podcast player. View our YouTube channel and rate us with five stars. If you liked this episode, you might also like Episode 9: The Fourth Industrial Revolution, post-COVID-19, Episode 4: A Renaissance in Manufacturing, or Episode 20: The Digitalization of Körber. Augmented - upskilling the workforce for industry 4.0 frontline operations.Special Guest: Çağlayan Arkan.