Episode 102: Lean Manufacturing with Michel Baudin
Augmented Ops - Un pódcast de Tulip - Miercoles
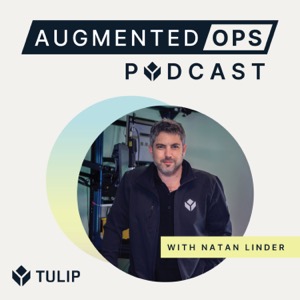
Categorías:
Augmented reveals the stories behind the new era of industrial operations, where technology will restore the agility of frontline workers. In this episode of the podcast, the topic is Lean Manufacturing. Our guest is Michel Baudin, author, and owner of Takt Times Group. In this conversation, we talk about how industrial engineering equals the engineering of human work and why manufacturing and industrial engineering education needs to change because it has drifted away from industrial work and a future where manufacturing is not going away. If you like this show, subscribe at augmentedpodcast.co. If you like this episode, you might also like Episode 84 on The Evolution of Lean with Professor Torbjørn Netland from ETH Zürich. Augmented is a podcast for industry leaders, process engineers, and shop floor operators, hosted by futurist Trond Arne Undheim and presented by Tulip. Follow the podcast on Twitter or LinkedIn. Trond's Takeaway: Lean manufacturing might mean many things, but industrial work has largely been a consistent practice over several hundred years, which is not necessarily a bad thing. Having said that, if we want to go about improving it, we might want to stay pretty close to the workforce and not sit in statistics labs far removed from it. Efficiency is tied to work practices, and they cannot be optimized beyond what the workforce can handle or want to deal with. As we attempt to be lean, whatever we mean by that, we need to remember that work is a thoroughly human endeavor. Transcript TROND: Welcome to another episode of the Augmented Podcast. Augmented brings industrial conversations that matter, serving up the most relevant conversations on industrial tech. Our vision is a world where technology will restore the agility of frontline workers. In this episode of the podcast, the topic is Lean Manufacturing. Our guest is Michel Baudin, author, and owner of Takt Times Group. In this conversation, we talk about how industrial engineering equals the engineering of human work and why manufacturing and industrial engineering education needs to change because it has drifted away from industrial work and a future where manufacturing is not going away. Augmented is a podcast for industrial leaders, process engineers, and shop floor operators hosted by futurist Trond Arne Undheim and presented by Tulip. Michel, welcome. How are you? MICHEL: Fine, thank you. How about yourself? TROND: Things are good. Things are looking up. I'm excited to talk about lean manufacturing with you, having had such a rich, professional background. Michel, you're French. You originally, I think, were thinking of becoming a probability researcher, or you were actually, and then you went to Japan and studied Toyota. You have had this career in English, German, Japanese sort of consulting all the way back from 1987 onwards on exciting topics, lean manufacturing, and especially implementing it, right? The real deal. You've authored at least four technical books that I know about. And I think you listed probably a while back, having written 900 blog posts. You've been very busy. You are the owner of the Takt Times Group, which is a consulting firm on lean manufacturing. And you love math, but you have this very interesting attitude, which we'll talk about, which is math is great, but it's not always the best communication tool. Tell me a little about that to start off. You're a probability researcher that doesn't use math; I think that's fascinating. MICHEL: I use it, but I don't brag about it with people that it turns off. So I have to be in the closet for this because people who work in manufacturing usually focus on concrete things, things that they can see and touch, and abstraction is not something that they respond well to. So whenever you explain a principle, my approach is to state this principle and then dig into some very specific examples right away; otherwise, I'm losing the people I'm talking to. But anyway, that's what I've had to do. TROND: So, did I capture your background okay? I mean, you've had a very international life so far. I hope it's been enjoyable and not just professional because you've spent your time in Germany, and Japan, and in the U.S., So you're really enjoying the different kinds of manufacturing environments. Or is it that you just want to be close to where it's all happening? MICHEL: I've enjoyed living in many different countries. And so you mentioned I'm French. I was born and raised in France, but I'm an American citizen, and I spent most of my life in the U.S. I think of myself as being part French, part American, part German, part Japanese. Because when I'm in a country, I tend to immerse myself in the culture; I don't stay aloof from it. TROND: Well, I'm curious about that because in the abstract... so if we are in the world of math, then you could maybe say that efficiency techniques are global; that was the idea. Some people have that idea, let's say, that efficiency is a global thing, and there's one thing called efficiency, and everybody should just learn it because then it's all better. It seems to me that because you spent a lot of time in three different places, it shows up differently. MICHEL: I don't use the word efficiency so much because it's limited. There are techniques to improve manufacturing performance in every aspect of it, efficiency only being one of them, and these techniques are pretty universal. Now, when you're trying to help people in different countries, it's a postulate. You have to postulate what works in one place will work in another. So far, I haven't found any reason to believe otherwise. I have encountered many people who are saying things like, "This is country X, and these techniques don't work because our people are from country X." It's one of the most common techniques to refuse to implement anything new. The fact is the Toyota Production System wasn't supposed to be applicable to American workers until Toyota applied it with American workers in its joint venture with GM in the early 1980s at NUMMI specifically. It became a showcase. Later, Toyota opened its own factory in the U.S. in Georgetown, Kentucky, and applied the system there. And then, a few years later, it opened its own factory in France, and it worked with French workers. So it's really the idea that this only works in certain cultures or this only works in Japan. It's just the reality is different. It works pretty much everywhere. TROND: Well, that's fascinating, though, because, like you said, you have immersed yourself in these different factory and industrial cultures, if you may, and you are implementing lean in all of them or advising on lean methods. Why don't we start with that, then, perhaps? Tell me a little bit, what is lean to you? MICHEL: Lean to me...and I use the term less and less because I think over the past 30 years, it's lost a lot of its meaning. When it first came out, it was the latest in a number of labels that have been applied to the same thing. In the early 1980s, you talked about just-in-time then there was world-class manufacturing. A number of different terms were used and never really caught on. This one caught on. And the way I took it, I took it to mean generic versions of the Toyota Production System. There are very good reasons why you can't call what you're proposing to a company that makes frozen foods a Toyota Production System. There are also very strong reasons why you can't even go to a car company and do this. It's very awkward for a car company to openly admit to be using a competitor's system. So you have to have a label that refers to the content but doesn't refer to where it's coming from. TROND: So for you, at the basic level, if you strip away everything, it still is essentially the Toyota Production System, and lean is just to you, I'm just paraphrasing, it's a convenient wrapping for a way to explain it in a way that's non-threatening. But it is essentially the lessons from the Toyota Production System from a while back. MICHEL: That's the way I took it. That's why I adopted this label in the early 1990s, but a lot of time has elapsed since then. Because it became popular, very many people started using that label. And the content they were putting under it was pretty much...they were attaching this label to whatever they were doing. It has lost a great deal of its meaning which is why at this point, I rarely refer to it. TROND: So you're saying a lot of people are attaching lean to whatever they're doing, I mean, understandably so, Michel, right? Because it's become a very successful term. It sells books. It sells consulting. It does refer back to something that you think is real. So can you understand why people would do this if you are in consulting, or even in teaching, or you work in an industry, and you're managing something, why people would resort to this label? MICHEL: First of all, consultants have to have a brand name for what they're selling. It was useful. As a brand name, you have to call what you're offering by a given name, and clients look for this. It's a keyword they look for, and that's how they find you. So it's really necessary. I'm not criticizing consultants for using that. TROND: No, no, I understand it. And, I mean, you're also a little bit in a glass box in the sense that you are within the general tent of lean yourself. So I understand that. I fully understand it. MICHEL: What happens when it's successful is that more and more people jump on this bandwagon and say, okay, I'm going to offer a lean. When you look at what they're saying, it does not reflect the original content. By about 2000s, it had evolved into...what most consultants were offering was drawing value stream maps and organizing Kaizen events. Those two keywords are absent from the Toyota Production System. TROND: Can you explain...so this is interesting. Because I was going to ask you exactly this, what are the types of elements that you react to the most that you feel is really...because one thing is to say it diverged from the original content, but if it is kind of a valuable extension of something...but you're saying value streams and the Kaizens, the Kaizen practices they have very little to do with the Toyota Production System in your reading. MICHEL: That's right. The value stream mapping is a new name for a technique that they call; I mean the translation of the original name is, Materials and Information Flow Analysis (MIFA), Mono to Joho no Nagare in Japanese, flow of materials and information. So that's one idea. And there is a particular graphic convention that has actually evolved from Toyota that became the value stream mapping graphic convention, but it never was in the Toyota context. Mike Rother's own admission (He wrote Learning to See, which promoted this technique.) said it was not an important topic at Toyota. It has some uses, but if you go on factory tours in Japan, you don't see a lot of value stream maps. And so it's been taken...it was a specific tool for a specific purpose like figuring out how to work with a particular supplier. And then it was made into this supposedly all-powerful analytical tool that is the first thing that you have to do when you go into a factory is map its value streams, so that's taking a very small part of what Toyota does and make it into this big thing. As for Kaizen Events, it's actually an American invention. It's something that came out of...in the early 1990s; there were a number of executives who were frustrated with the slow pace of lean implementation with other methods. So they came up with this format they called the Kaizen Blitz, that became the Kaizen events. It's also traced back to some Japanese consulting firms, which found this particular format as a convenient way to make good use of a trip from Japan to the U.S. They would organize one-week events at their clients because it was a good way to justify essentially the cost and the trouble of flying over. TROND: I'm going to go with your story here. So let's say these two are kind of examples for you of things diverting from the original content. Why don't we speak about what the original content then is for a minute? What is the core of the Toyota production method or of lean in its original form for you? MICHEL: Well, the Toyota Production System is something I'm very interested in and still studying. And it's not a static thing. It's something that, for example, the first publication about it was from the early 1970s, an internal document from Toyota with its suppliers. And then there have been many, many other publications about it through the decades. And it's changed in nature, and the concepts of manufacturing have evolved. By definition, the Toyota Production System is what Toyota does. They're very good at making cars. And so it's always important to try to keep up with what it is they're doing, knowing that there is a 5 to 10-year gap between the time they come up with new concepts and the time that the rest of the world gets to know about them. And so, in the early 1990s, there were essentially concepts of how to organize production lines, how to lay out production lines, how to design operator workstations. And there were concepts on how to regulate and manage the flow of materials and the flow of information between stations and lines and between suppliers and customers. And there was also an approach to the management of people and the whole human resource management aspect of hiring people for careers, having career plans for everybody, including shop floor operators, managing to improve the operations based on this infrastructure. So it's a very rich concept, and it encompasses every aspect of manufacturing, logistics, and production control, all the way to accountability. So it's compared with other things like the Theory of Constraints or TPM that are much more limited in scope. There is an approach to quality that Toyota has. The quality improvement is not all of the Toyota Production System. It's a complete system for making a product covering all the bases. TROND: Let me just pick up on one thing, so you're saying it's a complete system. So one thing you pointed out was the HR aspect, and hiring people for careers is one thing, but you also said the career plans for shop floor operators. So I took two things from that, and I was going to ask about this because this has been used as one example of why you cannot implement the Toyota Production System in the same way in different countries, namely because that is one aspect of society that a company doesn't fully control because it is regulated. So, for example, in Europe and in France, which you know, really well, and Germany, you know, employment is regulated in a different way. If a company was going to have the same HR policy in three different factories in three different countries, they would have to have, first of all, obviously, follow the national regulation. But then they would have to add things on top of that that would, you know, specific employee protections that are perhaps not part, for example, of U.S. work culture. So that's one thing I wanted to kind of point to. But the other thing is interesting. So you said career plans for shop floor operators meaning Toyota has a plan for even the basic level worker meaning the operators, the people who are on the floor. And that seems to me a little bit distinct. Because in the modern workplace, it is at least commonly thought that you spend more time both training and caring about people who are making career progression. And you don't always start at the bottom. You sort of hope that the smart people or whatever, the people who are doing the best job, are starting to advance, and then you invest in those people. But you're saying...is there something here in the Toyota Production System that cares about everybody? MICHEL: Yes. But let me be clear about something. The way Toyota manages HR is not something that there are a lot of publications about. There's probably a good reason for this is because they probably consider it to be their crown jewel, and they're not that keen to everybody knowing about it. A lot of the publications about it are quite old. But there's nothing in the regulations and labor laws of any country that prevent you from doing more for your employees than you're required to. TROND: That's a great point. That's a great point. MICHEL: So there are laws that forbid you from doing less than certain things, but they're not laws that prevent you from doing more. There is no rule that you have to offer career plans for production operators because there's nothing preventing you from doing it. In a completely different situation, a large company making personal products ranging from soap to frozen foods...I won't name what the company is, but they have a policy of not being committed to their workers. Essentially, if business is good, you hire people. If there's a downturn, you lay people off. They wanted to migrate from the situation where you have a lot of low-skilled employees that are essentially temps to a situation where they have higher level of qualification and fewer people. So the question is, how do you manage the transition? The way this company eventually did it in this particular plant was to define a new category of employee like, say, technical operator. And a technical operator will be recruited at higher a level of education than the general population of operators. They will be given more training in both hard skills and soft skills and the specific processes they're going to be running, and some additional training on how to manage the quality of these processes, that sort of thing. But at the level of a production operator, they will be put in charge of these processes. And this small group would be separate job categories than the others. And gradually, this evolves to a situation where you only hire into this group. You don't hire any more of the traditional operators. And then, you provide a transition path for the other operators to become members of that group so that over a period of time, gradually, the general population of less skilled, less stable operator shrinks. And you end up over a number of years with a situation where all of the operators that you have are these highly trained operators who are there for the duration. So that's one kind of pattern on how you can manage this kind of transition. TROND: Super interesting. Can I ask you a basic question? So you've been in this consulting part of this venture, you know, of this world for a long time. Where do you typically start? When do you get called, or when do you sign up to help a company, at what stage? What sort of challenge do they have? Do you visit them and tell them they do have a challenge? What is the typical problem a company might have that you can help with or that you choose to help with? MICHEL: There are a lot of different situations. One particular case was a company in defense electronics in the U.S. had a facility in Indiana, and they were migrating all this work to a new facility in Florida. What they told me...they called me in, and they told me that they wanted to take the opportunity of this move to change the way they were doing production. Generally, my answer to that would be, well, it's really difficult to combine a geographical change of facility with an improvement in the way you do the work. Normally, you improve first where you are. You don't try to combine transformation and migration. TROND: It's a funny thing, I would say. It seems like the opposite of what you should be doing to try to make one change at a time. MICHEL: But there were several circumstances that made it work. You can have general principles, and when you're in a real situation, it doesn't always apply. One is the circumstances under which they were doing this migration was such that the people in the old plant were in an environment where there was a labor shortage, so none of them had any problem finding jobs elsewhere if they didn't want to move to Florida. If they wanted to move to Florida, they could, if they didn't want to move to Florida, they had to leave the company, but there were plenty of other companies hiring around. And so there was not this kind of tension due to people losing their jobs and not having an alternative. And then, the transition was announced way ahead of time, so they had something like a 15-month period to plan for their transfer. And to my great surprise, the operators in the old plan were perfectly...were very helpful in figuring out the design for the new lines and contributed ideas. And there was no resentment of that situation. TROND: In this particular example and in other examples, to what extent is production, you know, process redesign a technology challenge, and to what extent is it a human workforce challenge? Or do you not separate the two? MICHEL: I try not to separate the two because you really have to consider them jointly. A technical solution that nobody wants to apply is not going to be helpful. And something everybody wants to apply but that doesn't work, is not going to be helpful either. So you have to consider both. And in this transition, by the way, between these two plants, most of the labor difficulties were in the new plant, not in the old one, because this plant became a section of the new plant. And none of the other lines in that new plant did anything similar, so it stood out as being very different from what all the other lines did. What all the other lines did is you had a structure that is common in electronics assembly where you have rows of benches at which people sat and did one operation, and then the parts were moved in batches between these rows of benches. And instead of that, we put cells where the parts moved one at a time between different operations. And it was also organized so that it could be expanded from the current volume of work to higher volume of work. And so a lot more went into the design. I was a consultant there, but I don't claim credit for the final design. It was the design of the people from the company. They actually got a prize within the company for having done something that was exceptionally good. And when I spoke with them a few years later, they had gone from having something like 20% of the space used for production in the new facility to having it completely full because they were able to expand this concept. MID-ROLL AD: In the new book from Wiley, Augmented Lean: A Human-Centric Framework for Managing Frontline Operations, serial startup founder Dr. Natan Linder and futurist podcaster Dr. Trond Arne Undheim deliver an urgent and incisive exploration of when, how, and why to augment your workforce with technology, and how to do it in a way that scales, maintains innovation, and allows the organization to thrive. The key thing is to prioritize humans over machines. Here's what Klaus Schwab, Executive Chairman of the World Economic Forum, says about the book: "Augmented Lean is an important puzzle piece in the fourth industrial revolution." Find out more on www.augmentedlean.com, and pick up the book in a bookstore near you. TROND: Michel, I know that you have a consulting life and a consulting hat, but you also have a teaching hat and a teaching passion. Why did you write this recent textbook which is coming out on Routledge this fall, I believe, with Torbjø Netland from ETH? It's an Introduction to Manufacturing but with a very specific kind of industrial engineering perspective. You told me when we talked earlier that there's a really specific reason why you wrote this textbook, and you have some very, I guess, strong views or worries about how manufacturing education, but perhaps the way it's taught really needs to change. And you feel like some schools are drifting away from the core. What's happening there? MICHEL: Well, industrial engineering as a discipline is about 100 years old, take or leave a decade or two. It started out as...the way I describe it is the engineering of human work in the manufacturing environment. And it expanded to fields other than manufacturing, even at the time of pioneers like Frank and Lillian Gilbreth. For example, we know the way operating rooms in hospitals work with the surgeon being assisted by nurses who hand all the tools to the surgeon; that particular form of organization is due to Frank and Lillian Gilbreth, industrial engineers who looked at the way operating rooms worked and figured that you really don't want to leave a patient with his belly open on the table while the surgeon goes to fetch the tool. You got to have some people giving the tools to the surgeon so that the surgeon can keep operating on the patient. It sounds obvious now, but it wasn't obvious in 1910. And so they were immediately some applications outside of manufacturing, but the bulk of the work was on manufacturing. And the way it's evolved, especially in the past few decades, is that it's gotten away from that focus on human work. And when you look at the research interests of the academics in this field, you find that it's completely dominated by operations research and math. TROND: So we're back to the math. [chuckles] So I find it fascinating that...well, you obviously have a deep insight into it, so you are sensitized to the challenges of overfocusing on one technical discipline as kind of the mantra and the fodder, I guess, the research data for all kinds of processes. I mean, why is math such a big problem, and what do you mean by human work in industrial manufacturing? Because to many people, the advanced work right now is about digitization, digitalization, and it has to do with machines and computers, and one would assume with big data or at least with data. Are you arguing against that trend? MICHEL: No. I mean, if you ask the question of what is human work? The classical answer that I would give is what happens when the guy picks up the wrench. That's one answer. But what happens when the operator sees an alarm message on the control screen of a machine, that's a different answer, a more modern answer. So you had people with the torque wrench applying the right torque to a bolt manually, and then the torque wrench would tell him when the torque was achieved. That's one form of human work. But monitoring and looking after multiple machines that are connected and have a central control system is also human work. You also have people doing it. And they have to feed these machines. They have to make sure that the machines have the right kinds of tools and dyes available to them. They have to maintain these machines. They have to program these machines, and they have to monitor them during production. And one particular problem with automatic systems is micro stoppages. Are you familiar with that term? TROND: Well, explain it to all of us, micro stoppages. I mean stoppages, obviously, anything that stops the production line, whether it's a minor, major, I mean, that would be what I think you are saying. MICHEL: Well, if it's a big problem, the operator doesn't solve it. The operator calls maintenance, and maintenance sends somebody to solve it. Micro stoppage is a problem that's small enough for the operator to deal with. And so, in daily life or in any office life, one very common micro stoppage problem is the copier, right? You tell the copier to print 20 collated copies of a document, and you walk away expecting to find these 20 copies ready when you come back. It doesn't happen because there are some paper jams and so you have to clear the paper jam and restart. You have a lot of things like that in production where parts jam and shoots and stop coming down in automatic system. You have all sorts of issues like this which cause production lines to stop in a way that the operator can resolve in half a minute or a minute and restart. What these things cause is that you have to have an operator there. And so if you really want to have an automatic system that are fire and forget...when you press a button, you move away to do something else while the machine goes through an automatic cycle. When that automatic cycle is finished, you come back. Micro stoppages prevent you from doing that. And they're very difficult to avoid, but they're a major problem, even today. TROND: Michel, I wanted to keep talking about the educational part. But before that, I just wanted to benefit from your experience here and ask you a much more basic question which is so you're writing this textbook about the future or introducing prospective students to industrial engineering and manufacturing. My question is, historically, factories were a very, very big part of manufacturing. Nowadays, meaning in the last few years after the pandemic and other things, a lot of us start to spend a lot more time on an issue, which I'm assuming you have spent a lifetime working on as well, which is supply chain which goes far beyond the factory because it's not located in any one factory, if anything, it's a system of many factories, and it's obviously the supplies of material flows into the factory. And the reason I'm asking you about this is in thinking about the future, which I'll ask you about in a second, a lot of people are sort of factory of the future, this and that. And there are visions about how this is going to change. But it strikes me that manufacturing is and has always been so much more than the factory. What are the components that you really worry about? So, humans, you worry about humans. And you worry about materials. And then you obviously have to worry about the physical infrastructures that are regulating these things. What else goes into it on the macro level? What is this book about, I guess? MICHEL: We're talking about supply chains as well because, as you mentioned, they're a very important part of manufacturing. And when you design a manufacturing system to make a product, you have to make decisions about your products, about components of your product, and what you make in-house, and what you buy from the outside. And there's a major difference between supply chain issues relating to customers, on one hand, the suppliers on the other. It's not just suppliers; it's both sides, incoming supply chain and the outgoing as well. One major difference with what happens in the factory is that you don't control what other people decide, what other organizations decide. So when you manage a supply chain, you have to manage a network of organizations that are independent businesses. How do you get this network of independent businesses to work with you, to cooperate with you, to make your manufacturing successful? That is a big challenge in supply chain management. Inside a factory, that's an environment you control. It's your organization. What management says is supposed to go; it doesn't always, but it's supposed to go. And you have a lot more control over what happens inside than over what happens in the supply chain. And how much control you have over what happens in the supply chain depends greatly on your size. For example, if you're a small customer of a special kind of alloy that only has one manufacturer in the world, you're a very small customer to a very large manufacturer, a metals company. You're not in a position of strength to get that supplier to work with you. If you're a car company making 10 million cars a year and you're dealing with a company that is making forgings for engine parts, you have a lot of control. You have a lot of influence. You represent a large part of their business. They can't afford to lose you. You can't afford to lose them. You can replace them if they don't perform. They can't afford to lose you. They might go out of business if they did. So it's a very different kind of position to be in. And so when you deal with that sort of thing, you have to think through, what is my position with respect to suppliers and customers? Where is it? Where's the driving influence? And it's not always...power in a supply chain is not always resident with the company that does the final assembly of consumer products. In electronics, for example, semiconductor manufacturers are much more key than people who assemble computers. TROND: I wanted to ask you a little bit about the trends and how these things are evolving in the next decade and beyond that. And one example you gave me earlier when we talked was pilots and jetliners because manufacturing in...well, the aviation industry is an example of an industry that, yes, it has an enormous amount of high tech. It's a very advanced science-based development that has produced air travel. But yet these pilots...and I experienced it this summer, a pilot strike stops everything. So the role of people changes as we move into more advanced manufacturing. But people don't always disappear. What do you see as the biggest challenge of manufacturing and the role of manufacturing in the emerging society? What is going to happen here? MICHEL: What I think is going to happen is that in many countries, the manufacturing sector will remain a large part of the economy, but as economies advance, it will have a shrinking share of the labor market. So it's a distant future, maybe like that of agriculture, where 2% of the population does the work necessary to feed everybody else. And manufacturing is now about 10% of GDP in the U.S., 20% in Germany and Japan, about 10% in England, France, Italy. In China, we don't really know because they don't separate manufacturing from industry. And industry is a broader category that includes mining, and it includes road construction, et cetera. They don't separate out manufacturing, but really, it's a big sector of the economy. And so it can remain a big sector, that's not a problem. But you have to think through a transition where the number of people that you employ doing this kind of work goes down, their level of qualifications go up, and the nature of the work they do evolves towards telling machines what to do and maintaining machines. So telling machines what to do can be programming machines when you develop processes, or it can be scheduling what work the machines do. TROND: Is that incidentally why you have gone into teaching in a kind of an academic setting or at least influencing curriculum in an academic setting so much that you see a role here in the future? Beyond what's happening in factories today, you're quite concerned about what might happen in factories ten years from now, 20 years from now when these students become, I guess, managers, right? Because that's what happens if you get education in management at a good school, reading your hopefully great textbook. It takes a little time because you trickle down and become a manager and a leader in industry. So I guess my question then is, what is it that you want these people to know ten years from now when they become leaders? What sort of manufacturing processes should they foster? It is something where humans still matter for sure, and machines will have a bigger part of it. But there's things we need to do differently, you think? MICHEL: The airline pilot metaphor, you know, you have this $300 million piece of equipment. And how much money you make from operating it depends on these two people who are in the pilot's cabin. You have to pay attention to the work of people. And in most factories, the work of people today is an afterthought. So you put in machines. You put in production lines without thinking how will people get from the entrance of the building to where they actually work? TROND: I was going to say it's a fascinating example you had with the airline industry in the sense that, I mean, honestly, even in the old industrial revolution, these machines were expensive, but I guess even more so. I don't know if you've done any research on this, but the amount of dollars invested per worker presumably has to go up in this future you are talking about here where we're increasingly monitoring machines, even these perhaps in the past viewed as low-skilled jobs or operator jobs. I mean, you are operating, maybe not airplanes, but you're operating industrial 3D printers that cost hundreds of thousands of dollars with presuming error rates that could be catastrophic, either for you, for the production line, or for the product you're making. MICHEL: Or photolithography machines that cost millions. TROND: Right. But then that begs the question for me, Michel, how on earth is it possible? If you are right about this that education has been somewhat neglected and skills has been neglected, how's that even explainable? If you are a responsible factory manager or executive of a large manufacturing firm, how could it have gotten...and I'm obviously paraphrasing here. I don't know if you think it's that bad. But how could it get this bad that you actually had to come out and say it's a massive problem? MICHEL: What happens is that you hear a lot about systems thinking, which, to me, it's pretty obvious there's more to a factory or more to a manufacturing system, to supply chain than the collection of its components; it's pretty obvious. And when you change the way a supplier delivers parts, it has an impact over what happens at the assembly workstations where these components are being used, for example. You have to think of the whole as a system. And you have to think about whenever you make any changes to it; you have to think through how these changes affect the whole. What's happening is that there has been a great deal of specialization of skills; I'm not talking about factory workers here. I'm talking about engineers and managers that have been put into silos where they run production control. They become production control manager in the factory. Their next career move is to become production control manager in the factory of a different company. TROND: So here's my open-ended question to you; you're sort of saying that industrial engineering, in one sense, needs to go back to its roots where it was. But the other side of the coin here is you're also talking about a world that's changing drastically. So my question is, the industrial engineer of the future, what kind of a person is this ideally, and what sort of skill sets and what sort of awareness does this person have? MICHEL: The skill sets that this person should have are both technical and managerial. It's management and technology considered together. So they may not be able to write code, or they may not be able to design how to cut a piece of metal, or how to tweak the electrical properties of a circuit, but they know the importance of these things. They've been exposed to them through their education and career. And they have an appreciation for what they are. So, for example, one particular task that has to be done in every manufacturing organization is technical data management. You have to manage the problem definition, the process definitions, which machines you use to do what, down to the process program that these machines run. All of this is data, technical data that has to be managed, put under revision control. And you'd expect someone with training in industrial engineering to understand the importance of revision control on this. If you change something to the cutting program of a milling machine, you may affect what happens elsewhere. You may affect the mechanical properties of the product and make it difficult to do a subsequent operation later. And that's why before you implement this change in production, you have to have a vetting process that results in revision management. So I would expect an industrial engineer to understand that. TROND: Well, you would expect an industrial engineer to understand that, but, I mean, some of the challenges that come from these observations that you're making here they impact all operators, not just engineers. And they certainly impact managers because they are about this whole system that you are explaining. So it sounds to me that you're mounting a pretty significant challenge to the future manufacturers, not just in skills development but in evolving the entire industrial system. Because if we're going to make this wonderful spacecraft, and solve the environmental crisis, and build these new, wonderful machines that everybody expects that are going to come churning out every decade, we certainly need an upskilled workforce, but we need a whole system that works differently, don't we? MICHEL: Yes. Can I give you a couple of examples? TROND: Yeah. MICHEL: One company outsourced the production of a particular component to a supplier then there were technical problems with actually producing this component with the supplier. So the customer company sent a couple of engineers to the supplier, and they found some problems with the drawing that had been provided to the supplier. And they made manual corrections to the drawings, the copies of the drawing in possession of the supplier. And it worked. It solved the immediate problem. But then, at the customer company, they didn't have the exact drawing. The only place with the exact drawings was at the suppliers. And a few years later, they wanted to terminate this supplier. TROND: Aha. MICHEL: You can see the situation. You want people to be able to understand that you just don't do that sort of thing. TROND: Right. So there are so many kinds of multiple dependencies that start to develop in a manufacturing production line, yeah. MICHEL: And then you find a company that's a subcontractor to the aircraft industry. And you find out they route parts through a process that has about 15 different operations. And the way they route these parts is they print a traveler that is 50 pages long, and it's on paper. And the measurements they make on the parts that they're required to make by their customer they actually record by hand on this paper. What's wrong with this picture? TROND: So yeah, multiple challenges here. MICHEL: Yes. TROND: Are you sensing that these things are fixable? Are you optimistic in terms of this awareness of all aspects of the systems changing both among managers and next-generation industrial engineers, and perhaps even among the operators themselves to realize they're getting a more and more central role in the production system? MICHEL: I won't try to prophesy what will happen to industry as a whole but what I'm confident about is that the companies that know how to address these problems will be dominant. Those are the sort of basic mistakes that really hurt you and hurt your competitive position. So there will be a selection over time that will eliminate people who do these kinds of mistakes. TROND: Michel, I don't want to put you on the spot here. And you have spent your career researching and tracking Toyota as an excellent, excellent manufacturer that has graciously taught other manufacturers a lot. And also, people have copied and tried to teach them Toyota methods, even if Toyota wasn't trying to teach everyone. Are there any other either individual companies or things that you would point to for the eager learner who is trying to stay on top of these things? I mean, so lean, obviously, and the Toyota Production System is still a reference point. But are there any other sources that in your career or as you're looking at the future where there is something to learn here? MICHEL: Oh yes. Toyota is a great source of information, but it's by far...it's not the only one. One of the key parts of Toyota's management system is Hoshin Planning. Hoshin Planning didn't come from Toyota; it came from Bridgestone tires. And so that's one case where a different company came up with a particular method. Honda is a remarkable company as well, so there are things to learn from Honda. HP was, under the leadership of its founders, a remarkable company. And they had their own way of doing things which they called The HP Way. Companies have recruited a lot of people...electronic companies have recruited a lot of people out of HP. And you feel when you meet the old timers who have experienced The HP Way, they feel nostalgia for it. And there were a lot of good things in The HP Way. They're worth learning about. So I also believe that it's worth learning about historical examples because history is still with us in a lot of ways. The Ford Model T plant of 100 years ago was a model for a lot of things at the time. It also had some pretty serious flaws, namely, its flexibility. And you still see people putting up the modern-day equivalent of a Model T plant with new products and new technology but without thinking about the need. That particular plant may have to be converted in the not-too-distant future into making a different product. So it's always worth looking at examples from 100 years ago, even today, not for the sake of history but because, in a lot of ways, history is still with us. TROND: Well, on that note, history is still with us; I thank you for this, Michel. And I shall remember to forget the right things, right? So history is still with us, but [laughs] you got to know what to remember and what to forget. Thank you so much. MICHEL: Culture is what remains once you've forgotten everything. TROND: [laughs] On that note, Michel, thank you so much for your time here and for sharing from your remarkable journey. Thank you. MICHEL: You're welcome. TROND: You have just listened to another episode of the Augmented Podcast with host Trond Arne Undheim. The topic was Lean Manufacturing. Our guest was Michel Baudin, author, and owner of The Takt Times Group. In this conversation, we talked about how industrial engineering equals the engineering of human work and why manufacturing and industrial engineering education needs to change because it has drifted away from industrial work. And indeed, we are looking at a future where manufacturing is not going away. My takeaway is that lean manufacturing might mean many things, but industrial work has largely been a consistent practice over several hundred years, which is not necessarily a bad thing. Having said that, if we want to go about improving it, we might want to stay pretty close to the workforce and not sit in statistics labs far removed from it. Efficiency is tied to work practices, and they cannot be optimized beyond what the workforce can handle or want to deal with. As we attempt to be lean, whatever we mean by that, we need to remember that work is a thoroughly human endeavor. Thanks for listening. If you liked the show, subscribe at augmentedpodcast.co or in your preferred podcast player, and rate us with five stars. If you liked this episode, you might also like Episode 84 on The Evolution of Lean with Professor Torbjørn Netland from ETH Zürich. Hopefully, you'll find something awesome in these or in other episodes, and if so, do let us know by messaging us because we would love to share your thoughts with other listeners. The Augmented Podcast is created in association with Tulip, the frontline operation platform connecting people, machines, devices, and systems used in a production or logistics process in a physical location. Tulip is democratizing technology and empowering those closest to operations to solve problems. Tulip is also hiring, and you can find Tulip at tulip.co. Please share this show with colleagues who care about where industry and especially where industrial tech is heading. To find us on social media is easy; we are Augmented Pod on LinkedIn and Twitter and Augmented Podcast on Facebook and YouTube. Augmented — industrial conversations that matter. See you next time.Special Guest: Michel Baudin.