Episode 101: How Academia Shapes Manufacturing with John Hart
Augmented Ops - Un pódcast de Tulip - Miercoles
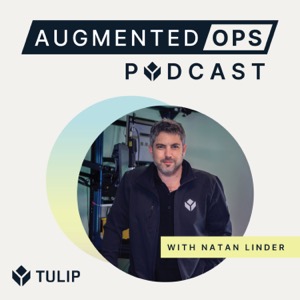
Categorías:
Augmented reveals the stories behind the new era of industrial operations, where technology will restore the agility of frontline workers. In this episode of the podcast, the topic is "How Academia Shapes Manufacturing". Our guest is John Hart, Professor of Mechanical Engineering and Director at the Center for Advanced Production Technologies at MIT. In this conversation, we talk about John's research on micro and nanotechnology and material science, which universities and colleges that teach manufacturing, the role of MIT in this ecosystem, and why now is a key moment in manufacturing history. If you like this show, subscribe at augmentedpodcast.co. If you like this episode, you might also like Episode 92 on Emerging Interfaces for Human Augmentation. Augmented is a podcast for industry leaders, process engineers, and shop floor operators, hosted by futurist Trond Arne Undheim and presented by Tulip. Follow the podcast on Twitter or LinkedIn. Trond's Takeaway: There has never been a more interesting time to be in manufacturing or to watch manufacturing. The tremendous breakthroughs that we are about to witness have been made possible by a confluence of emerging technologies and startup innovations, as well as a growing awareness of the importance of building human-centric technologies. We are indeed at a crossroads with profound challenges in the growing talent shortage, the need for workforce training, an aging industrial base, and the demands for manufacturing competency from the wider innovation ecosystem. We have to make progress fast, and innovations are just maturing to be able to do so at the scale and pace required. It will, again, be amazing to watch the manufacturing industry. Parts of it will perhaps, again, become the industry of industries. Transcript: TROND: Welcome to another episode of the Augmented Podcast. Augmented reveals the stories behind the new era of industrial operations where technology will restore the agility of frontline workers. Technology is changing rapidly. What's next in the digital factory, and who is leading the change? And what are the skills to learn and how to stay up to date on manufacturing and industry 4.0. In this episode of the podcast, the topic is How Academia Shapes Manufacturing. Our guest is John Hart, Professor of Mechanical Engineering and Director at the Center for Advanced Production Technologies at MIT. In this conversation, we talk about John's research on micro and nanotechnology and material science, which universities and colleges that teach manufacturing, the role of MIT in this ecosystem, and why now is a key moment in manufacturing history. Augmented is a podcast for industrial leaders, for process engineers, and for shop floor operators hosted by futurist Trond Arne Undheim and presented by Tulip. John, how are you? Welcome. JOHN: I'm well, Trond. Great to see you. Thank you for having me. TROND: Well, I'm excited to have you talking about...well, hopefully, a lot of different things, but how academia gets to shape manufacturing, this fascinating venture that is manufacturing. But you yourself, John, you grew up in Michigan, is that right? You were close to this from an early age. JOHN: I was close to it. Yeah, I grew up in Royal Oak, Michigan, a suburb north of Detroit. If you know the Detroit Metro area, there are the mile roads, and the Detroit River is sort of Zero Mile. And I grew up between 14 and 15 Mile Roads, so in the hotbed of the good, old U.S. auto industry. TROND: Well, exactly. Because looking a little bit at your background here, you spent quite a few years as a summer intern at General Motors before you got yourself to...or actually perhaps in the beginning, in your undergrad years from UMichigan, is that right? JOHN: I did. After my first year at UofM, I worked as a summer intern at GM and went back a few years in a row in different roles in different areas. And honestly, when I decided to pursue a graduate degree and ended up at MIT, I thought I might just get my master's and go back and work in the auto industry, but things changed, and here we are today. TROND: Well, here we are today. You got yourself an undergrad from UMichigan. And you worked there for a little while, I believe, but then came to MIT with a master's, Ph.D. This is way back. But you won the prize for the best doctoral thesis in micro and nanotechnology. So that set you off on the path to rediscover nanomaterials, I guess. JOHN: Yeah, well, it's a really maybe exotic combination of topics. My master's thesis was on precision machine design, the design of these large mechanical couplings for industrial robots. And then, for my Ph.D., with the same advisor, I worked on carbon nanotube synthesis. But there you have the dipoles of manufacturing research, materials, processing, and mechanical design that have shaped how I've taken things forward since then. TROND: Well, but it is in these unique combinations that innovation starts to occur, right? JOHN: Yeah, exactly, combining different topics. And that's one reason I love manufacturing is that it is the union of materials processing, and automation, and software, and now also getting more interested in the organizational workforce aspects. It's a very rich, multidisciplinary layered topic. TROND: Yeah. And we'll explore this both from the organizational angle, and, indeed, I'm super interested in this material angle on things because it seems to me like you're exploring the very, very small nanostructures, but then you're then printing them on the very large canvas. So you're exploring materials from one extreme to the other. JOHN: Yeah. Well, it depends on your objective and what topic you're working on. There are cases in our research where we need to understand the formation of materials, not quite from the atom up but from the nanoscale or microscale up. And there are cases where we more or less abstract or coarse grain those link scales and focus on macroscale properties. TROND: Well, and then you also focus quite a bit on teaching. I noticed that you actually launched the first massive online course on manufacturing processes, and hopefully, we'll get to this a little bit as well. JOHN: Sure. TROND: But teaching and basically working on the next generation of manufacturers, whether they be the engineers or really anybody else, has certainly been one of the big challenges in manufacturing really forever. What is it that fascinates you so much about teaching this to a grander audience than the usual university audience? JOHN: Well, first, I'll say I believe that the top priority of universities, including in the area of manufacturing, is to educate future leaders and engineers. That said, the number of people we educate on our campus is a small fraction of those who could really benefit from what we teach and the way we teach. And that's not just geographically, but it's also in terms of their role in the workforce. So I believe manufacturing education should address all levels of the workforce. And to get at your question more directly, when I came to MIT, I was asked to take over our core undergraduate manufacturing class in the Department of Mechanical Engineering. And as I learned to teach the class for myself, I was intrigued by this emerging trend of digital learning, and this was 2015, 2016. And I was able to get some funding from MIT internally to create an online version of the course that would be offered free to the world, and probably 100,000 People have taken it so far. And it's been a great experience and evidence of how there is very broad interest in manufacturing really across the world. TROND: 100,000 people have taken this course. JOHN: Yeah. Well, I'll say 100,000 people have signed up for the course. This is the classic trade-off with online courses. It doesn't mean 100,000 people complete the course. It means that number signs up and hopefully took something away from it. It also speaks to the flexibility. You can sign up for a course and maybe just listen to one lecture, but if you take something valuable away from it, that's great. TROND: So I wanted to talk a little bit about how academia shapes manufacturing. And I know that there are, you know, you and I work at MIT, and you've had experiences obviously at University of Michigan. But there are other manufacturing centers and institutes all around the world. Could you lay out this landscape a little bit for us so that we get a sense of where the excellent centers of manufacturing are located? I mean, one structure, just to pick that, is manufacturing institutes, and I know that's sort of dear to your heart for a couple of different reasons that we'll get into. But what are some of the centers beyond MIT where there is activity that is organized in a way that really is something to focus on? JOHN: First, I think of in the U.S., Carnegie Mellon, Georgia Tech, Purdue, Michigan, Stanford, places that have defined manufacturing centers or have a body of work that relates to manufacturing that I would say there's a critical mass of faculty, and students, and affiliation with industry. Also, Penn State in the area of additive manufacturing and product design. It's hard to be comprehensive. I don't want to forget anyone big, but that's a sample of some of the notable ones. Internationally, a lot of activity in Europe; I admire the University of Cambridge, the Institute for Manufacturing there, where manufacturing is more or less a department, or it's within the Department of Engineering, which is analogous to what we would say is a school or college of engineering here in the U.S. And they have a broad set of activities that have been there for decades focused on manufacturing at the IFM. TROND: And if you think about the best schools to get educated in this topic, is it necessarily only the top brands? I mean, certainly, they have different roles. So when it comes to undergrads or even shorter, or I guess even community colleges have a really fundamental role in the formation of this sector, can you talk a little bit about that? JOHN: Oh, for sure. When you think of manufacturing education, we must think of the full stack of institutions that educate the workforce, from vocational institutions to community colleges where the student's goal may just be to complete a vocational program or complete a two-year degree and then exit the workforce, all the way to the four-year degrees, advanced degrees, and executive education. And given how manufacturing is paramount in the workforce and the economy, we need to educate folks at all those levels. But by far, the largest number of people are at those vocational community college levels and then to the bachelor's level. So I have a Ph.D. I love to mentor Ph.D. students. But that's a small fraction of the manufacturing workforce. TROND: What about in the U.S. setting? There's something called the Manufacturing USA, and there are these institutes that have sponsorship from various government agencies, most of them through the Department of Defense. But there's also a bunch at the Department of Energy and one, I guess, from the Department of Commerce. What is the role of basically government-sponsored sort of research and innovation activities in this field? It would strike me, I guess, that historically, it's quite important. JOHN: Certainly. You're alluding to the manufacturing innovation institutes, the MIIs that were started during President Obama's administration. Actually, MIT's work, the Production in the Innovation Economy study, and the Advanced Manufacturing Partnership, which emerged from that, was key in scoping the MIIs, and now there are 16 or so around the country. It's one example of public-private partnership. Public-private partnership is key to cultivating interest in manufacturing and also providing resources for technology translation and commercialization. I think the MIIs have had a great impact on awareness of manufacturing, on R&D, and really applied research in some critical technology areas. But it's only a small part of what we need to do to regrow and expand our industrial base in the U.S. TROND: So I want to move us shortly to MIT to discuss both your own research activity and how extensively you are now aiming to take a more organizing role to kind of get more out of all of the exciting work that's happening at MIT. But before that, I just spotted perhaps an older project of yours that I thought was extremely cool. You were once called a nanoartist, and you had this NanoArt Nanobliss gallery with visualizations. You previously mentioned Obama. I believe you made a NanoArt structure called Nanobama or something of that sort. How did this come about? And, again, I mean, I'm guessing this just sort of testifies to your interest in science communication as much as in the depths of science, which we'll get into in a moment. JOHN: You got it. The inspiration was how do we communicate what we're doing in the lab to broader audiences just to make them aware of what's happening in new technology, new materials? In that case, it was nanotechnology. If you don't mind, I'll tell you a bit more of the story. When I was an assistant professor at Michigan, we were doing a lot of work on carbon nanotube manufacturing, which was a follow-on from my graduate work at MIT. And I admired President Obama, or he was a presidential candidate at that time. And without implying a political inclination, I somehow put together the words nano and Obama in my mind. TROND: [laughs] JOHN: And I said, wow, it would be cool to have a Nanobama. So one thing led to another, and I actually worked with some students in my group to fabricate these little portraits out of carbon nanotubes representing Shepard Fairey's portrait of Obama that was used widely during that first presidential campaign. And I just posted it online, I think one day after the election, and it took off. It went viral, so to say, and was featured as Nature's Image of the Year. It was printed on the newspapers you used to get as you walk onto the subway in the morning around the world. There was a company that would syndicate this stuff, and they just sent it around. So it got a lot of attention. And it showed me the power of an image in communicating something. And, of course, President Obama, that was a historic election. The play on words was exciting, and also the fact that it was a little bit intriguing science and technology that was nano was interesting. And one more thing, a colleague of mine at Michigan then was working in the White House, and he said, "Hey, can you send us a Nanobama?" So I made this frame with a little piece of the real material, and a picture of it from the microscope sent it to Washington. I didn't hear anything about it until I got a call from the White House asking me to declare the value for the President's tax return because he decided to keep it; I kid you not. And then, after Obama left office, I was with my family at a bookstore in Wellesley, and I saw the book, the retrospective book of Pete Souza, the White House photographer. And I opened up the book, and I see a picture of Obama and John Boehner in the Oval Office in the middle of this book. And right on the doorframe is the Nanobama. So it actually made it to the White House, which was a pretty awesome feeling. TROND: It must be an awesome feeling, and, again, I think that, especially in this field of manufacturing which is so challenged at times, right? And people are talking about how these factories are greedy, or is this a great job, or whatnot. And there have been all of these historical moments. But then there is also this fascination around the topic of certainly of technologies and the excitement around it. Why don't we continue a little bit on this strand before we get into sort of the overall role of MIT? I'm really curious about how your research has evolved. So generally, I get that you're combining these nanostructures with manufacturing and materials research, and certainly, you have applied it to additive manufacturing. How would you say that your research has evolved over these years? What are the things that you have been doing? I've picked up on a few things that I definitely wanted to cover. I mean, certainly, you've been working on this industrialization of 3D printing, both as a research area and as a commercial area. Carbon nanotubes must have been kind of where you started. I'm curious where that work is going. And then I saw that very recently, with a student, you've been doing some work that I'm personally very enthused about, which is a plant-derived composite that might replace, hopefully, plastics with sort of a hardness and stiffness that is somewhere at the boundary between conventional plastics and metals. I mean, for me, I don't quite see how all of these things are intimately connected. Where do you go for, you know, where's my next proposal here, and where's my next patent? JOHN: They aren't necessarily closely connected. But I like to say that the themes are typically one or more of materials, manufacturing, and mechanical systems or automation. And what I love about manufacturing, especially in the materials domain, is to control a process, to understand a process, and then to do something new, you need to investigate its fundamentals. And sometimes, you need to design a new instrument or machine to get the job done. So our work is often problem-inspired or opportunity-inspired. Like, the cellulose work that you mentioned recently was actually sponsored by a large consumer products company interested in a more sustainable composite material that could be used in packaging. And we looked at potential routes to formulating different materials, and we landed on cellulose. And then, we developed a formulation, a mixture of cellulose nanocrystals and polymers that ended up having exciting mechanical properties, particularly very high hardness, and toughness, more so than existing polymers. And another unifying theme is scalability. It's important not to worry too much about scalability in the early stage of research, and there's lots of amazing research that's just for science. But we like to do things that we hope will be scalable one day, so choosing ingredients that would be cost-effective or using techniques that could be industrialized, even if the techniques look very different in the lab. And maybe I've lacked to give a precise definition or focus, but I think it's also indicative of the broad span of manufacturing. And manufacturing has many, many dimensions beyond the ones that we work on in my lab at MIT. TROND: Well, you kind of answered a question that I was going to ask, too, which is it doesn't seem like you start in a linear fashion, you know, in other words, you start with some sort of basic problem that everybody in their literature has established and then you move to this, that, or the other. Sometimes it comes from a company. The challenge comes from a company, but you formulate the solution completely. It seems to me that students also have lots of ideas and kind of formulate projects. Talk to me a little bit about this process of where the problem comes from versus where the solution and impact comes from because you seem to...sometimes the output truly is just, you know, like, in this case, art or a physical prototype, and you're sort of happy with that outcome. Other times, you're actually delivering something into, presumably, eventually, an assembly line. JOHN: Yeah. And we work as hard as we can on technology translation, both in terms of the knowledge that we publish but also in terms of the steps that we take to spin technology out. You're right; the early stage is very important. And I like to often see the early stage as a collaboration between myself and the researchers. And in many cases, the core idea we end up pursuing comes largely from the research or the research team. In many cases, it might be seeded by the interest of a sponsor or an idea I have, and then we work together on actually figuring out what's the approach, what are the outcomes, and what's the path to success. MID-ROLL AD: In the new book from Wiley, Augmented Lean: A Human-Centric Framework for Managing Frontline Operations, serial startup founder Dr. Natan Linder and futurist podcaster Dr. Trond Arne Undheim deliver an urgent and incisive exploration of when, how, and why to augment your workforce with technology, and how to do it in a way that scales, maintains innovation, and allows the organization to thrive. The key thing is to prioritize humans over machines. Here's what Klaus Schwab, Executive Chairman of the World Economic Forum, says about the book: "Augmented Lean is an important puzzle piece in the fourth industrial revolution." Find out more on www.augmentedlean.com, and pick up the book in a bookstore near you. TROND: You have commercialized at least two ventures together with others at MIT and external people as well that I know about for sure. I wanted to just briefly mention both Desktop Metal and VulcanForms. Let's perhaps cover Desktop Metal first, so that's a 3D printing company. Tell me how that got started and what your role was there. JOHN: So I was very fortunate to be a member of the founding team of Desktop Metal. So there were seven co-founders, and we launched the company in early fall of 2015. And Ric Fulop, who's the lead founder and CEO, approached me at that time, and he heard that I was interested in working on 3D printing and, of course, knew a bit about my background in manufacturing and machine design and asked me to jump on board. And funny story, how just connections persist over the years; I actually knew Ric when I was a grad student because I was doing my carbon nanotube work using the space of now my colleague, Yet-Ming Chiang. And at that time, Yet and Ric were launching A123 Systems, a successful battery company. So that was a reason why I think Ric knew to get in touch with me when he heard about me. And serendipity was a great experience. TROND: Serendipity when you are in the right places, right? If you're hanging around Yet-Ming Chang, yeah, that's right, very special serendipity. Tell me a little bit about VulcanForms. Until very recently, you couldn't talk so much about it. Nowadays, you did go out in New York Times. I've read that piece. So there is a little bit more detail around it. Let me ask a very basic and perhaps dumb question, large-scale metal 3D printing, what's the big deal there? I thought didn't Desktop Metal do 3D printing? So it's kind of a dumb question. Why is there a second company? Is there really such a variety? I think that the regular person just thinks 3D printing is 3D printing. JOHN: 3D printing is a broad and deep subject. Like, first of all, 3D printing processes exist for polymers, for metals, for many other materials. And there are even several 3D printing technologies for metals. I'll tell the origin story for VulcanForms quickly if that's okay, and then get back to the question. So when I came to MIT as faculty in 2013, I had been a professor at Michigan for a few years. And I landed, and one of the topics I thought of looking into was 3D printing. I was actually asked by a colleague to teach a class not on 3D printing, but I was able to propose the topic. And in that class, there were many incredible students. One of them, named Martin, stuck around at MIT after finishing his master's in manufacturing, and we ended up comparing notes and launching VulcanForms in 2015, a little bit before Desktop Metal came to be, but not that long before. And we stayed quiet for seven years. We raised our seed round a couple of years ago. And the focus of the company is number one, laser-based metal additive manufacturing. And second, while we've built our own additive technology, we're a manufacturing company. So we produce parts at scale, and that is a real need and has been a barrier to growth of the additive industry. There's so much interest and uptake in additive. But the ability to achieve high-quality production using additive as the formative step in the process at scale has largely been untouched. So from the early days, we thought that we could approach the market with that plan to become a manufacturing company. TROND: Staying quiet for seven years that can't have been [laughs] particularly easy. JOHN: Yeah, it's not easy, but it's very, very worth it because we got to focus. And also, there are different boundary conditions that allow you to keep your head down and get work done, and one of them is having great and patient investors who believe in your approach and who see the progress behind the curtain. And as a result, we felt we would hold off launch. And we were fortunate to get picked up by the New York Times earlier this summer. And now we're excited to talk about what we do. TROND: Yeah, that article did hint a little bit at what your printers can print that others cannot and kind of at what scale. Can you give some examples of the kinds of things that you are now contracted to print or are perhaps already printing? JOHN: So the company is focused on a variety of industries, generally industries where high-value metal parts are difficult to manufacture and where there is a real pent-up need for more agile, high-value manufacturing medical devices such as medical implants, semiconductor components, not microchips but cooling devices for various computer systems. We have a lot of business in the aerospace and defense area, working with several of the defense primes, both on additive parts and on machining, honestly. The company, as described in the New York Times article, we acquired a machine shop in Newburyport, Massachusetts, earlier this year. And that was twofold, one because in order to deliver finished parts, you need to often integrate additive with machining. So it's not just 3D printing; it's building a stack of software and physical processes to create a finished part. Second, advanced machining is also a digital manufacturing technology, and as a company, we're very interested in applying our capabilities as a digital manufacturing organization to the area of CNC machining as well. TROND: So, taking that experience then from these two companies and your vast interest and research area plus your interest in communication, what is it that you're now focused on at MIT more largely? That's another kind of secret that's slowly being let out. But you have had this notion and have shared this with me and others, obviously. There was a seminar open to whoever was invited, I think, but not a full public launch. Manufacturing at MIT has historically been quite important, but you think that there's even more, to be done. You lined up a couple of the projects, but there are many more things that MIT has done. Could you maybe just briefly address the role of MIT historically in influencing manufacturing? And what else is it that you now want to accomplish? JOHN: Yeah, for sure. And since I came to MIT nine years ago, I've learned of the incredibly rich history that the institute has in manufacturing, both on the technology side, you know, in the mid-1950s, building among the first CNC machines, ultimately transformed commercial aviation in 1980 building one of the first 3D printers in the world, and so on. But not only that, but also, historic accomplishments in the social sciences, understanding the globalization of manufacturing, you know, what delineated the U.S. versus the Japanese auto industry in the 1980s. What is the intrinsic role of manufacturing in innovation, the production, and innovation economy led by my colleague Suzanne Berger in around 2010. And then broader than manufacturing, though, the work of the future study just a couple of years ago looking at the connection between technology and work. So looking at all those accomplishments and understanding the present moment that we're in, which I can also reflect on later, I've been exploring how to create a new presence for manufacturing at MIT. And the term manufacturing at MIT is more or less a placeholder representing the community of faculty and students across disciplines, both technology and social sciences, that touch on all the dimensions of manufacturing. So as we've returned from Zoom life to more in-person life, I've been making my way around campus and building a team of folks, faculty advisors, external advisors, industry partners, and so on to hopefully put forward a new center at MIT that has a focus on manufacturing across the disciplines. And this is not to replace existing activities but just to augment those activities and bring industry together with us to support research, to lean deeply into workforce training programs, to collaborate with public organizations at the state and federal level and internationally, and also hope to cultivate more entrepreneurship. Because my experience, fortunate experience as an entrepreneur over the past several years tells me that there's opportunity for more new companies that contribute to the future of manufacturing, whether they're manufacturing companies actually making stuff, whether they be software and services companies. Or perhaps the biggest need is hardware companies for whom manufacturing is a route to success. So you may not be manufacturing something yourself, or you may not be manufacturing goods for others, but understanding manufacturing and scaling a process is really key. And that intellectual DNA of manufacturing is more cross-disciplinary than ever. And I've observed over my nine years at MIT how there's just more engagement in manufacturing as a discipline, as this cross-disciplinary theme. And that's an area where I feel such a center can really play a role by adding something to the intellectual community across the institute. TROND: There are so many things that come to mind when you produce this narrative because, I guess, on the one hand, manufacturing is a little bit of everything. On the other hand, it is clearly very delineated because it's all about making things and making them at scale. And there's a whole industry, but, of course, every industry almost has a manufacturing arm. How do you delineate the subject of manufacturing? And I'm sort of curious, you know, at MIT, if you use a broad church definition, almost everybody there contributes to manufacturing. So that would be both a challenge and an opportunity, I guess. JOHN: Yeah, you're exactly right. So, first, within MIT, we have many collaborations with different departments and other research centers. And the nature of the collaboration depends on what the focus is. Second, when it comes to interfacing with industry, I've come to look at industry as kind of a grid where you could say the columns are the end users, say, aviation and space or consumer or construction. And then, the horizontal lines in the grid are technologies, robotics and automation, 3D printing, software and IT, et cetera. And getting a little bit in the weeds of the organization here, so first, we're working on launching a flagship industry consortium, or we're recruiting flagship industry partners for a new center. And those will be companies, world-leading manufacturing companies across the grid. Second, we will operate consortia in different technology in industry areas that may be located within our center that may be in collaboration with others around MIT to really drive focus. And when industry comes and interacts with us, I want them to understand how their business fits into the broader spectrum. And we find particularly in the work related to 3D printing that companies appreciate being connected with peers across the value chain. They say 3D printing is materials at the frontend and finished parts at the backend, and there are some machines and software, and so on. When you bring companies together across their value chain, across their supply chain, under the umbrella of an academic organization with this sort of problem-solving mindset, we find that that can be valuable to the companies that we partner with. TROND: And, John, there's obviously a scale at MIT that's hard to replicate for any university or school just because there are so many people involved in technical innovation. But on the other hand, I would say there has been a sense that other sectors if you could call them that, have always been moving much faster than manufacturing. And, you know, okay, fine, there are industrial revolutions, but the ones we talk about now as industrial revolutions are more, you know, they are maybe on the software side and stuff, but that the core of manufacturing it may be because of its inherent nature. It's complex; it's about physical infrastructure, at least a lot of it still. So it's hard to innovate in that sector. Would you say that one of the ambitions you have with this manufacturing at MIT initiative is to speed up that innovation? And if so, what are the mechanisms that would bring manufacturing as a whole, I guess, on an even faster sort of clip? JOHN: First, if I look within MIT, we see the opportunity to combine the physical side, the mechanical engineering, the material science, with the digital side, with software, and controls, and computation. And that's an area where it's clear that new technologies can be de-risked, can be scaled more quickly. And it really requires this symbiosis of the physical processes and the digital intelligence. Second, I think we can do better research. I can do better research by understanding where the big problems and opportunities are. And by connecting closely with industry, forming networks with various stakeholders, we can define better problems that we can ask our students to solve. And third, I've noticed, especially over the past year with all the geopolitical discussions and the imperative for sustainability, that we're at a time where there's this alignment between industry and government and the investment community and manufacturing, physical manufacturing, physical industry is vital. We can't do enough there to catch up, to grow. And I think that's a real opportune moment to recognize that while I think the pendulum has swung to the digital world and software over the past 10, 20 years, life has changed for the better in so many ways. We have to focus on the physical world now, especially to address the climate crisis, and also think of how we can improve economic equality across our communities, how we can provide better job opportunities, how we can deliver education to individuals who don't have the opportunity to go to university or don't have the resources to travel, all those things. So that's another reason why, one, I see manufacturing as this rich, cross-disciplinary topic that I can file a patent and write some exciting papers and graduate with a Ph.D., but it means so much more to feel technology at scale. And second, you need the intersection of these disciplines to understand not just technology but organizations and human dynamics to create change and create positive impact. TROND: So I realized that we're going to have to cover... there are so many other questions I have for you is what I'm trying to say here. But my last question in this round, I think, is going to be one on...we briefly mentioned, or you briefly talked about augmentation. And you know that I have a special interest; obviously, the topic of the podcast and the title is augmentation. So there is something here about the tension, perhaps between augmentation and automation. How do you see that tension or the relationship between working from the human-centric perspective that technologies are in service to perhaps augment people and processes versus this automation perspective which maybe takes, and I'm paraphrasing here, a little bit more of an efficiency approach and tries to go for machine scale first and then just adjust everything later? How do you see those two things now, as perhaps, you know, manufacturing is coming into another kind of growth moment? JOHN: If I understood you correctly, I don't think they're mutually exclusive, right? Certainly -- TROND: No. Not necessarily. Not necessarily. JOHN: Certainly, manufacturing will become more automated in places where automation makes sense. Certainly, automation is challenging to implement to scale, to get right. But in some cases, the driver to more efficient technology-first manufacturing is automation. In other cases, and hand in hand with that, human workers and businesses, organizations can only become more effective and efficient, working in synergy with data and automation. I'll use the example of someone overseeing a 3D printer, a state-of-the-art 3D printer, and watching the screens to make sure everything is going well and doing a better job by being presented with information that shows, hey, this might be a problem, or there are no problems here, but being empowered to make that data-driven decision. And also, from my work outside of MIT, we find that folks who do best operating that advanced equipment with digital data might have a machining background. They might also have a passion for gaming on the side. So they might be used to sensing and responding to dynamic digital events. And that's another comment on skills evolving in the workforce too. TROND: Well, I mean, one thing that is for certain is that if MIT gets its act together on manufacturing, things will happen. I trust that we're going to have to come back and talk about a lot of emerging projects here in the coming years if you get people lined up. So very exciting. Thank you for speaking to me. Is there sort of a challenge that you want out there to the community when it comes to how, you know, not just academics can contribute to shaping manufacturing but how we all should think of these manufacturing challenges? Is it something that we should leave to experts right now because it's so complicated? Or are there ways that the broader interested public can get engaged in this problem? Is it possible to engage, and where should one engage? JOHN: That's a great question. First, to the general public, I'd say stop and think about what manufacturing means to you, or find one of your favorite things and look up how it’s manufactured. Imagine the life, the journey of the product as it comes to your door. And second, I'd say the area where most of us can make an impact is in education and learning and contributing to our communities. Perhaps if you're an engineer working somewhere, you might want to teach at a community college one night a week if you have time in a future semester or explore ways that you can bring new knowledge, new technology to your organization if it makes sense. TROND: Exciting challenges. Thank you so much for sharing a little bit of what you're up to with us, John. JOHN: Thank you, Trond. TROND: You have just listened to another episode of the Augmented Podcast with host Trond Arne Undheim. The topic was How Academia Shapes Manufacturing. Our guest was John Hart, Professor of Mechanical Engineering and Director at the Center for Advanced Production Technologies at MIT. In this conversation, we talk about John's research on micro and nanotechnology and material science, which universities and colleges that teach manufacturing, the role of MIT in this ecosystem, and why now is a key moment in manufacturing history. My takeaway is that there has never been a more interesting time to be in manufacturing or to watch manufacturing. The tremendous breakthroughs that we are about to witness have been made possible by a confluence of emerging technologies and startup innovations, as well as a growing awareness of the importance of building human-centric technologies. We are indeed at a crossroads with profound challenges in the growing talent shortage, the need for workforce training, an aging industrial base, and the demands for manufacturing competency from the wider innovation ecosystem. We have to make progress fast, and innovations are just maturing to be able to do so at the scale and pace required. It will, again, be amazing to watch the manufacturing industry. Parts of it will perhaps, again, become the industry of industries. Thanks for listening. If you liked the show, subscribe at augmentedpodcast.co or in your preferred podcast player, and rate us with five stars. If you liked this episode, you might also like Episode 92 on Emerging Interfaces for Human Augmentation. Hopefully, you'll find something awesome in these or in other episodes, and if so, do let us know by messaging us. We would love to share your thoughts with other listeners. The Augmented Podcast is created in association with Tulip, the frontline operation platform that connects the people, machines, devices, and systems used in a production or a logistics process in a physical location. Tulip is democratizing technology and empowering those closest to operations to solve problems. Tulip is also hiring, and you can find Tulip at tulip.co. To find us on social media is easy; we are Augmented Pod on LinkedIn and Twitter and Augmented Podcast on Facebook and YouTube. Augmented — industrial conversations that matter. See you next time.Special Guest: John Hart.